Understanding OEE: The Key to Manufacturing Efficiency
Blog
4 Min Read
In today’s competitive manufacturing landscape, improving efficiency and productivity is crucial for businesses to remain competitive. One of the key metrics used to measure manufacturing efficiency is OEE or Overall Equipment Effectiveness. In this blog, we will take a closer look at OEE and its importance in manufacturing.
What is Overall Equipment Effectiveness (OEE)?
Overall Equipment Effectiveness (OEE) is a metric that measures the effectiveness of manufacturing equipment. The OEE metric is widely used in manufacturing industries to identify areas for improvement and to measure the effectiveness of production processes. OEE score is a percentage that is calculated by multiplying three factors: Availability, Performance, and Quality. Each factor is expressed as a percentage.
OEE can be used to identify areas for improvement in manufacturing processes. By analyzing the three factors that make up the OEE score, manufacturers can identify the root causes of inefficiencies and quality issues and take steps to address them. This can include implementing preventive maintenance programs, improving changeover processes, upgrading equipment, and implementing quality control measures.
The formula for OEE is: OEE = Availability x Performance x Quality
Let’s take a closer look at each factor:
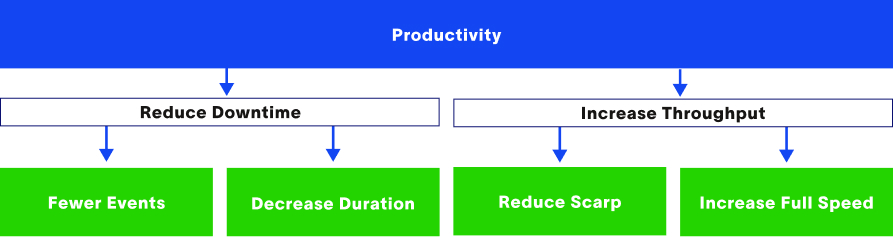
High OEE vs Low OEE
A high OEE indicates that the manufacturing equipment is operating at its maximum potential in terms of availability, performance, and quality. A high OEE means that the equipment is producing high-quality products efficiently and with minimal downtime. This results in lower manufacturing costs, higher productivity, and increased profitability.
On the other hand, a low OEE indicates that there are problems with the manufacturing equipment or the production process. This may be due to factors such as breakdowns, low operator efficiency, low-quality products, or other issues that are affecting the overall effectiveness of the equipment. A low OEE means that the equipment is not operating at its full potential and that improvements need to be made to increase productivity, reduce downtime, and improve product quality.
In summary, a high OEE is desirable as it indicates that the manufacturing process is efficient, effective, and profitable, while a low OEE indicates that there are problems that need to be addressed in order to improve efficiency, productivity, and profitability.
Importance of OEE in Manufacturing
OEE is an important metric for measuring manufacturing efficiency for several reasons:
Provides a clear picture of equipment performance:
OEE provides a clear and objective measure of how well equipment is performing. It allows manufacturers to identify areas where equipment is not performing optimally and take corrective action to improve efficiency and productivity.
Customization and personalization
Industry 4.0 technologies allow businesses to offer customized and personalized products and services to their customers. With the help of digital technologies such as 3D printing and digital twins, businesses can create unique products tailored to individual customers’ needs and preferences.
Better decision-making
Industry 4.0 technologies provide businesses with real-time data and analytics, enabling them to make better decisions. This helps businesses identify and solve problems quickly, improve processes, and respond to changing market conditions.
Improved safety
Industry 4.0 technologies such as robotics and automation can help reduce the risk of workplace accidents and injuries. By automating hazardous tasks, businesses can create a safer work environment for their employees.
New business models and revenue streams
Industry 4.0 technologies can enable businesses to create new revenue streams and business models. For example, businesses can use IoT sensors to collect data on how their products are used and offer new services based on this data.
Sustainable practices
Industry 4.0 technologies can help businesses reduce their environmental impact. For example, by using predictive maintenance to reduce equipment downtime, businesses can reduce energy consumption and greenhouse gas emissions.
Roadmap to improving your OEE performance
Increasing OEE performance is a continuous improvement process that requires a roadmap or plan that includes the following steps:
- Identify the current OEE score and analyze the contributing factors:
The first step in increasing OEE performance is to determine the current score and analyze the factors contributing to it. This will help you understand the areas that need improvement and prioritize actions. - Second step: Proof of Concept
The Proof of Concept (PoC) phase aims to showcase the value of the proposed solution, instill confidence in the overall MES approach, and justify further investment and development. After conducting an MES Assessment, a collaboration between stakeholders is needed, to identify and prioritize a set of high-priority requirements to be developed for a specific production area. For instance, we may develop Production and Performance Reporting for a Packaging Line or Paperless Quality for a Mixing Area. This approach enables you to make informed decisions at each stage of the process, avoiding costly solutions that fail to meet customer needs. You can request our Agile MES Workshop to learn more about this approach. - Set clear goals and targets
Based on the analysis, set clear goals and targets for each of the three factors of OEE (Availability, Performance, and Quality) to improve the overall score. - Improve availability
The first factor of OEE is availability, which measures the percentage of time that the equipment is available for production. To improve availability, you can take measures such as implementing a preventive maintenance program, reducing changeover times, improving operator training, and implementing a spare parts inventory program. - Improve performance
The second factor of OEE is performance, which measures the rate at which the equipment is producing parts or products compared to its maximum potential. To improve performance, you can take measures such as optimizing production schedules, reducing stoppages, minimizing speed loss, improving process control, and upgrading equipment. - Improve quality
The third factor of OEE is quality, which measures the percentage of good parts or products produced by the equipment compared to the total number of parts or products produced. To improve quality, you can take measures such as implementing a quality control program, improving process control, training operators, and reducing defects and scrap. - Implement data analytics
To continuously monitor and improve OEE performance, it is important to implement data analytics. This involves collecting and analyzing data from the equipment, processes, and quality control systems to identify areas for improvement and track progress. - Continuous improvement
OEE performance improvement is a continuous process, and it is important to continuously monitor and improve the three factors of OEE. This can be achieved through ongoing data analysis, operator training, equipment upgrades, and process improvements.
In summary, increasing OEE performance requires a systematic approach that involves analyzing the current score, setting clear goals and targets, improving availability, performance, and quality, implementing data analytics, and continuous improvement. By following this roadmap, manufacturers can optimize their manufacturing processes, increase efficiency, reduce downtime, and improve profitability.
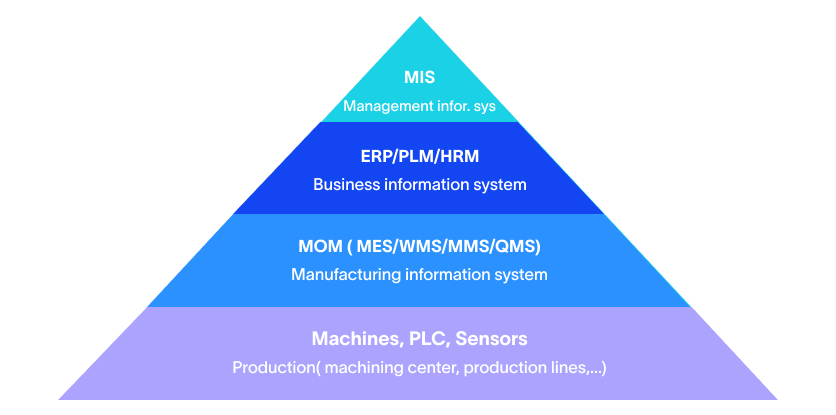
Agile MES: The Key to Unlocking Smart Manufacturing Success
MES is a computerized system used in manufacturing operations to track and document the transformation of raw materials into finished goods. An MES system typically manages and monitors work orders, equipment, materials, and personnel on the shop floor. The system provides real-time visibility into production processes, helps optimize manufacturing operations, and improves the overall efficiency of the manufacturing process.
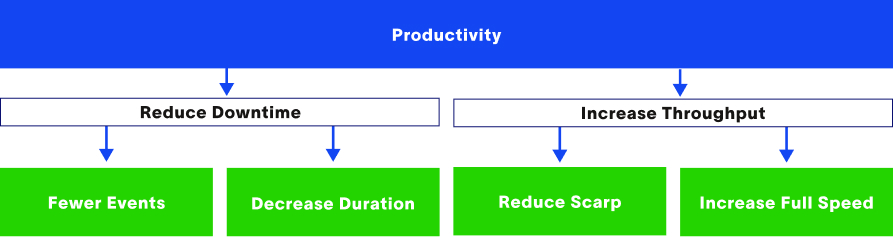
Understanding OEE: The Key to Manufacturing Efficiency
In today’s competitive manufacturing landscape, improving efficiency and productivity is crucial for businesses to remain competitive. One of the key metrics used to measure manufacturing efficiency is OEE or Overall Equipment Effectiveness. In this blog, we will take a closer look at OEE and its importance in manufacturing.
How to Effectively Conduct a Legacy System Integration
Legacy system integration can be a daunting task, but it’s a necessary one for many manufacturers that rely on outdated systems to run their business. Integrating legacy systems with modern technology can improve efficiency, streamline processes, and save time and money. However, it’s important to approach the integration process carefully and methodically to ensure success.
Share on :
Keep On Reading
Subscribe to Our Newsletter
Subscribe to our weekly newsletters to get updates regarding our new production, behind the scene process of our art creation and much more.
After submitting this form you will receive an e-mail with a confirmation link that you must click to complete your request. Detailed information on processing and cancellation can be found in our privacy policy.