The Smart Factory Playbook: A Step-by-Step Guide for Executives
Blog
6 Min Read
The manufacturing industry has evolved massively – from steam engines to assembly lines to automation. Now, we are at the doorstep of the fourth industrial revolution, driven by Smart Manufacturing and smart factory solutions. These factories use AI, IoT, and real-time data to self-optimize processes, reduce downtime, and maximize ROI of an organization.
So, in this guide, we’re going to break down the transition from conventional methods to using AI in manufacturing. Let’s begin.
Smart Factories – A Brief Overview
A smart factory isn’t just about having machines running on their own. It’s about using industrial automation solutions that make manufacturing faster, smarter, and more efficient. These factories IoT, AI, and real-time data to improve production while cutting expenses.
The key characteristics of a smart factory usually includes –
Automation and Robotics – Machines Working without Human Input
Robots, in this case, generally focus on handling repetitive, manual tasks and completing them as soon as possible. On the other hand, AI in manufacturing improves accuracy of these pieces of technology. This, in turn, results in faster production and less downtime.
Read our full guide on Future-Proof Your Manufacturing Operations with Real-Time Data and take the first step toward smarter, data-driven decision-making!
IoT and Connectivity
The IoT sensors can be used for collecting real-time data in order to help factories track performance, spot issues, and adjust operations almost instantly. The connectivity between them ensures that the tasks are completed without being too haphazard.
AI and Machine Learning
AI can help in predicting failure before they even happen. Machine learning, on the other hand, improves the quality of regular equipment checks and helps AI make smarter decisions without human intervention. Both of these technologies can also streamline processes together.
Digital Twins and Predictive Maintenance
A digital twin, in essence, is a virtual model of a machine or a factory. By integrating AI with it, you can predict breakdowns, test newer processes, and optimize efficiency. Predictive maintenance, conversely, reduces downtime and cuts down on costly repairs.
Cybersecurity and Data Protection
A connected factory, especially if you are also trying to make it smart, needs a strong security system. Smart factory solutions, thankfully, can protect sensitive data from cyber threats and make sure that your operations are smoother and safer than before.
Smart Factory: The Infrastructure
A smart factory runs on data, automation, and intelligent systems. However, in order to make it work, you’ll need to find the right technology and use it in unison.
For example, IIoT in manufacturing uses different types of sensors to track machine health, performance, and production in real-time. Cloud computing, on the other hand, stores and processes information remotely while edge computing analyzes it instantly on-site.
The latter is usually faster than the former, but cloud is also more scalable than edge computing. So, you have to use them collaboratively to make the most out of these two modern technologies.
But that’s how the basic technologies work in a smart factory. But what about the infrastructure? How should you establish it? Keep reading to find out more about it.
Unparalleled Connectivity
When you are working on creating a smart factory, the first thing you need to focus on is creating an ecosystem where machines can seamlessly communicate with each other.
This can be done through IoT-enabled technologies, like actuators and sensors, which transmit information to cloud platforms and central servers for analysis.
Strong Hardware Components
There are four types of industrial automation solutions that you need to include in a smart factory –
- IoT sensors for data accumulation
- Industrial robots for integrating automation
- Edge computing devices for local processing
- Networking equipment to support seamless connectivity
Apart from this, you should also use a security system to protect whatever data you are working with. The better the equipment you’re using, the more effectively your smart factory will work.
Software and Related Tools
Data analytics platforms are extremely important for analyzing the huge amount of data generated by a smart factory. Besides these, you’ll also need to invest in connectivity tools, such as middleware and APIs to facilitate communication between different tools and systems.
Scalability
The infrastructure of your smart factory should be scalable enough so that it can accommodate future growth in technological advancements and data growth. This might involve upgrading your older servers or adopting new cloud-based solutions for better flexibility.
The Unified Namespace (UNS): Why Data Integration is the Key
While building a smart factory comes with various challenges, the most important one among them all is data integration. Thankfully, a UNS (Unified Namespace) can help you out in this regard.
How Does UNS Work?
A Unified Namespace is a type of framework that aggregates information from different sources into a centralized data framework. This helps in improving consistency, accuracy, and a single source of truth – which can be accessed by everyone in the organization.
The technology does this by creating a virtual layer that brings different data systems together. This can be accessible through one interface by using software and data virtualization tools.
It can also extract information from –
- Different databases
- Applications
- Storage repositories
UNS focuses on syncing and updating data in real-time to make sure that all users and applications can access current data. It does so by combining the following software & hardware solutions –
- A platform to manage the UNS
- An edge platform with software APIs, device, and network connections
- Connections to PLCs, smart sensors, and enterprise applications
- MQTT data broker who will transfer information between the UNS database & its connections
- A secure, managed cloud data service or central SQL database
Benefits of a Unified Namespace
UNS tools usually integrate information from all sources into a single repository. This offers an end-to-end visibility into your data and helps you analyze the same comprehensively.
Besides, with Unified Namespace, your data will be continuously synced and updated in real-time. It, in turn, can improve operational responsiveness and allow you to react quickly to changes, find out issues in the machinery, and optimize processes on the go.
Also, by harmonizing data formats and standards across various systems, UNS can improve data consistency and reliability. The flexibility of this system also simplifies the integration of new systems, technologies, and applications to enable users to incorporate new technologies easily.
How to Implement Unified Namespace?
When it comes to integrating a Unified Namespace, there are four steps you need to follow closely. Here’s what you need to know about them –
- Establish data governance procedures by determining the type of data you want to manage
- Define a consistent structure for managing data across different systems and sites
- Implement appropriate mechanisms, like identity and access management, for security
- Standardize data representation by using different protocols
How to Prepare for Smart Factory Transformation?
Developing smart factory solutions from the ground up requires a solid plan and an expert to guide you through the entire process. Here’s how the roadmap looks like –
Understanding Your Current State
Before you start upgrading, take a step back and ask yourself a few questions first –
- What kind of systems have you already put into place?
- Are all of them working as intended or not?
- Is there any outdated system that’s slowing down your production level?
So, prior to implementation, it’s important to find out weak spots in your manufacturing ecosystem and make sure that Industry 4.0 technologies can improve all of them.
Setting a Vision and Goals
Start the integration procedure with small steps. We’d suggest automating a single process first and then planning for bigger changes, like full-scale digital transformation in manufacturing. Also, while you’re choosing the technologies, make sure that your investments match the goals of your organization, including – cost savings and faster production.
Building a Good Team
A successful smart factory transformation will require trained people from the IT, operations, and finance departments. So, try hiring the right people and training them in new tools, automation, & ML. This way, it’d be easier for them to stay on board and collaborate as required.
Smart Factory Transformation and INS3
Smart factory integration can be quite tricky, even if you have hired the right personnel. So, if you are looking for someone who can help you get in the right direction, INS3 can be the right partner for you. Here’s how we can offer our assistance –
Comprehensive System Integration Services
INS3 offers a suite of exclusive services tailored to facilitate digital transformation in manufacturing. Here’s what it may include, considering the range of your project –
- Establishing robust systems to connect different machinery, collect, share, and store data
- Upgrading your existing systems to modern standards and improve data flow
- Implementing manufacturing execution system to provide real-time information
- Transforming raw data into actionable insights to help you make data-driven decisions
Tailored Approach
At INS3, we use proven processes to guide manufacturers through the digital transformation journey. Here’s how we do it –
- Discovery: In this phase, we identify inefficiencies and issues currently plaguing your manufacturing ecosystem and find potential areas for improvement.
- Pathfinder: After that, our team develops a phased strategy to improve efficiency, quality, and cost-effectiveness of the manufacturing processes you’re using.
Conclusion
By collaborating with our team, manufacturers can navigate the complexities of smart factory implementation effectively. We can also help you achieve sustainable growth and competitiveness in the industrial landscape and stay far ahead of your competitors.
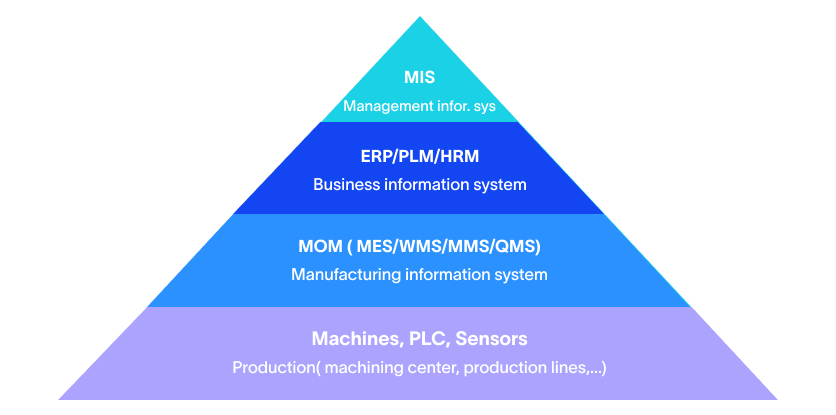
Agile MES: The Key to Unlocking Smart Manufacturing Success
MES is a computerized system used in manufacturing operations to track and document the transformation of raw materials into finished goods. An MES system typically manages and monitors work orders, equipment, materials, and personnel on the shop floor. The system provides real-time visibility into production processes, helps optimize manufacturing operations, and improves the overall efficiency of the manufacturing process.
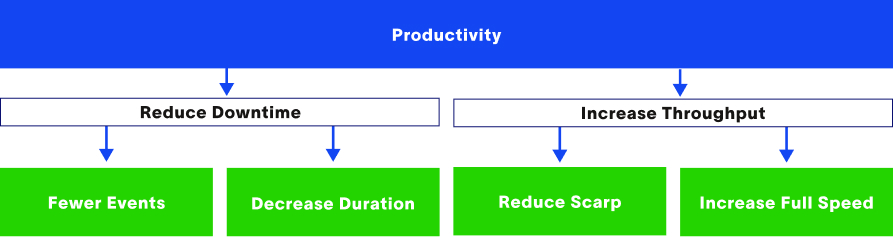
Understanding OEE: The Key to Manufacturing Efficiency
In today’s competitive manufacturing landscape, improving efficiency and productivity is crucial for businesses to remain competitive. One of the key metrics used to measure manufacturing efficiency is OEE or Overall Equipment Effectiveness. In this blog, we will take a closer look at OEE and its importance in manufacturing.
How to Effectively Conduct a Legacy System Integration
Legacy system integration can be a daunting task, but it’s a necessary one for many manufacturers that rely on outdated systems to run their business. Integrating legacy systems with modern technology can improve efficiency, streamline processes, and save time and money. However, it’s important to approach the integration process carefully and methodically to ensure success.
Share on :
Keep On Reading
Subscribe to Our Newsletter
Subscribe to our weekly newsletters to get updates regarding our new production, behind the scene process of our art creation and much more.
After submitting this form you will receive an e-mail with a confirmation link that you must click to complete your request. Detailed information on processing and cancellation can be found in our privacy policy.