How to Future-Proof Your Manufacturing Operations with Real-Time Data
Blog
5 Min Read
Real-time data equips you to fine-tune your manufacturing operations. It helps enhance efficiency with the power to make swift yet informed decisions.
The core of modernization in manufacturing lies in the ability to see through intangible aspects of machines, such as their uptime, production rates, and quality metrics. Real time data in manufacturing is the tool that gives you this ability.
This helps carve a personality for manufacturing operations by providing access to data of a machine’s every move in real time.
Moreover, digital transformation in manufacturing with Internet of Things (IoT), artificial intelligence (AI), and cloud computing this data gets extra wings. You can enable predictive maintenance to mitigate downtime and enhance overall productivity.
In this guide, we will talk about the usage of real time data in manufacturing and how it enables smart manufacturing solutions.
The Cost of Delayed Decision-Making in Manufacturing
Delayed decision-making in manufacturing has huge financial impact that leads to loss of value.
In manufacturing operations, delays can lead to extended labor costs, lost opportunities, the release of subpar products, and a damaged reputation. Hence, the ability to take prompt decisions is what leads your manufacturing unit to profit from all the available resources. Moreover, each manufacturing operation has different implementation times and values. A staggered flow of operations thereby leads to potential revenue loss in the following forms:
Ongoing Operational Costs
Resources are wasted while decisions are pending, as inefficient systems incur higher expenses.
Lost Opportunities
Delays can lead to missed market opportunities, allowing competitors to gain an advantage.
Erosion of Potential Value
Delayed decisions may decrease the value of opportunities over time, especially in rapidly changing markets.
Increased Risk
Longer decision timelines expose organizations to market volatility, leading to potential losses.
Disturbing the Organizational Inertia
Prolonged indecision can foster a culture of hesitancy, stifling innovation and proactive initiatives.
Nevertheless, you can future-proof all operations with real time data in manufacturing. Integrating manufacturing data analytics with predictive maintenance in manufacturing, your operations can run perpetually without facing delays and revenue losses.
How Real-Time Data in Manufacturing Transforms Operations Management
To processing real time data in manufacturing, you need a digital assemblage. This digital assemblage helps you enhance operational efficiency. Here are some of the transformative changes that you can bring with smart manufacturing solutions:
- Detect anomalies to make immediate adjustments and minimize downtime and operational disruptions.
- Analyzing machine conditions like temperature and vibration to forecast equipment failures.
- Ensure continuous quality control as sensors monitor critical parameters, triggering alerts for any deviations.
- Optimize resource utilization by tracking the use of raw materials, energy, and labor, identifying inefficiencies, and suggesting improvements.
- Improve inventory management, minimizing waste and reducing excess stock costs.
Hence, if you’re looking to scale up your manufacturing unit to meet the demands of the modern market, updating every process with real time data in manufacturing is the key.
But what technology can make that happen? In the next part we will talk about the three most important technological systems that make up for the best parts of industry 4.0. We’ll talk about its implementation and how you can establish this trio power to upgrade your manufacturing business.
Learn more about how data analytics helps minimize waste and boost efficiency in manufacturing.
SCADA + MES + IIoT: The Power Trio for Digital Transformation in Manufacturing
The greatest achievement of industry 4.0 has been in its creation of a virtual twin for every production process. So far, we had the machines, up and running, and now, we have achieved the ability to see how these machines run, in real-time, up until the product comes to existence and beyond.
This is where we can put the triple power of SCADA, MES and IIOT to fine-tune manufacturing processes and produce the best results for every function.
What is SCADA?
SCADA, or Supervisory Control and Data Acquisition, is the system for controlling, monitoring, and analyzing industrial processes with real time data in manufacturing. It employs hardware and software components, such as the following to collect data from industrial equipment and machinery:
- Programmable logic controllers (PLCs).
- Remote terminal units (RTUs).
- Sensors.
- Human-machine interfaces (HMIs).
All these components, together, enable remote monitoring and control of industrial processes, with real-time data analysis and presentation. Thus, you can manage complex production systems that would otherwise be hard to control manually
What is MES?
A Manufacturing Execution System (MES) is a computer program that monitors, regulates, and optimizes factory-floor manufacturing activity.
It is an intermediary between enterprise systems such as ERP and shop-floor activity, and it offers real-time information to improve efficiency, quality, and compliance.
MES systems monitor the conversion of raw materials into finished products, controlling resources like materials, labor, and equipment, and providing traceability and quality control.
Moreover, they facilitate in-depth scheduling, dispatching, and performance analysis, allowing manufacturers to determine bottlenecks and make fact-based decisions to enhance overall equipment effectiveness (OEE) and minimize downtime.
MES is especially important in highly regulated industries such as pharmaceuticals and food processing, where compliance and documentation are paramount.
What is IIoT?
Industrial Internet of Things (IIoT) is the interaction of intelligent machines, sensors, and devices, interconnected across the internet. It helps with predictive maintenance in manufacturing operations to make them smarter.
With the real time data in manufacturing, you can share your data to empower production optimization and efficiency and save costs at the same time.
Quality monitoring, automation, predictive servicing, and optimized supply chains are just some IIoT deployments for manufacturing.
IIoT, with machine-to-machine communication and analysis of big data, improves decision-making, lowers downtime, and boosts productivity.
It is one of the building blocks of Industry 4.0 that seeks to revolutionize production by combining physical manufacturing with smart digital technology.
Integrating SCADA, MES and IIoT for Real Time Data in Manufacturing
SCADA, MES, and IIoT integration needs architectural solutions focused on free data exchange, interoperability, and real-time decision-making. Below are the major architectural approaches defining this integration:
Converged SCADA-MES Platforms
You can integrate SCADA and MES into a single platform to eliminate data silos and ease development for manufacturing process optimization. This solution employs a single interface (e.g., Inductive Automation’s Ignition) to integrate SCADA’s real-time control with MES’s production monitoring and analytics.
Middleware-Based Integration
Using middleware (e.g., enterprise communication buses or IoT gateways) to connect data from legacy protocols (Modbus, Profinet) to more modern IIoT/MES systems.
Workflow will be: IIoT devices → Middleware (protocol conversion) → MES/SCADA systems.
Gateway-Mediated IIoT Integration
Here, IIoT industrial gateways serve as brokers. They collect machine/sensor data and forwarding it to SCADA or MES via standard protocols.
Hybrid Edge-Cloud Architectures
This integration process for real time data in manufacturing blends edge computing (data processing on-site) with cloud platforms (AWS IoT Core, Azure IoT Hub) for scalable storage and predictive analytics for manufacturing.
In this process, SCADA manages real-time control, while MES/IIoT manage batch processing and predictive information.
Hence, the data Flow will be: Edge devices process data in advance → Cloud for advanced analytics → MES/SCADA for action at the right time.
INS3 Case Study: Peanut Butter Manufacturer Transitions to Cloud-Based ERP
Challenge:
A peanut butter manufacturer faced significant concerns about moving to a cloud-based Enterprise Resource Planning (ERP) system. Their key challenges included the following:
- Potential cloud unavailability.
- Connectivity issues.
- Need to maintain operational continuity in their 24/7 production environment.
Solution:
To address these challenges, we upgraded their Manufacturing Execution System (MES) with enhanced features to manage production flexibility.
We implemented Electronic Data Interchange (EDI) for efficient order processing to the cloud, enabling real-time adjustments to production plans.
This integration also improved tracking of raw materials and finished goods, ensuring quality control and operational sustainability, even while remote work conditions persisted during the COVID-19 pandemic.
Results:
The transition resulted in notable improvements:
- 10-15% increase in first-pass quality
- 10% reduction in product downgrading
- 10-15% savings in utilities
- 5% decrease in waste
- Substantial reductions in scheduling disruptions
We were successful in helping this manufacturer avoid potential revenue loss from connectivity disruptions, saving them thousands of dollars per hour during such events, while maintaining smooth operations around the clock.
Challenges of Integrating these Smart Manufacturing Solutions
Nothing comes without challenges. Given below are some of the common roadblocks for integrating SCADA, MES and IIoT for Real Time Manufacturing Data:
- Interoperability: Old protocols (Modbus) versus new standards (OPC UA) need gateways or middleware to translate.
- Scalability: IIoT’s massive data volumes call for edge/cloud infrastructure upgrades.
- Security: Protocols such as OPC UA have encryption, but broken architectures leave them more vulnerable.
- All this is greeted by manufacturers with the adoption of these strategies—single visibility, less downtime, and increased agility—vital to Industry 4.0
Conclusion
Deploying a real-time data strategy to manufacturing involves a systematic approach. It begins with setting business objectives to support corporate goals in general, then infrastructure analysis and determination of related data sources.
Hence, a data governance model is essential to have data quality and security, while collecting real time data in manufacturing and integrating the same via tools give rise to a unified operational picture.
Through real-time manufacturing data analytics, you can facilitate your decision-making power by tracking production lines and identifying anomalies. Moreover, you can apply predictive maintenance in manufacturing to anticipate equipment failure and immediate quality control measures.
Hence, becoming a part of the 4th industrial revolution, you can track your performance continuously in real time with the triple power of SCADA, MES and IIoT to fine-tune your operational efficiency.
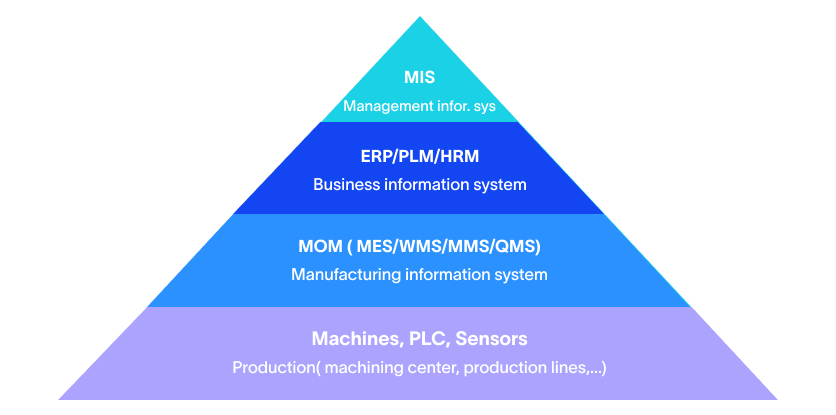
Agile MES: The Key to Unlocking Smart Manufacturing Success
MES is a computerized system used in manufacturing operations to track and document the transformation of raw materials into finished goods. An MES system typically manages and monitors work orders, equipment, materials, and personnel on the shop floor. The system provides real-time visibility into production processes, helps optimize manufacturing operations, and improves the overall efficiency of the manufacturing process.
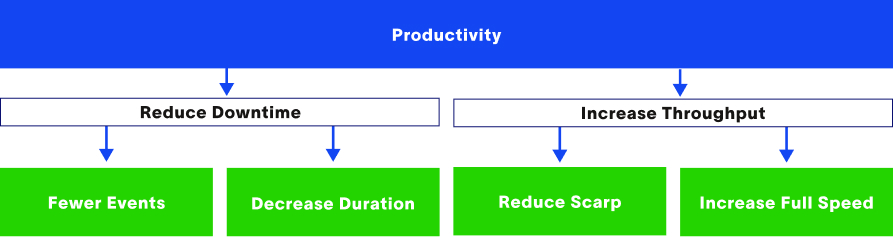
Understanding OEE: The Key to Manufacturing Efficiency
In today’s competitive manufacturing landscape, improving efficiency and productivity is crucial for businesses to remain competitive. One of the key metrics used to measure manufacturing efficiency is OEE or Overall Equipment Effectiveness. In this blog, we will take a closer look at OEE and its importance in manufacturing.
How to Effectively Conduct a Legacy System Integration
Legacy system integration can be a daunting task, but it’s a necessary one for many manufacturers that rely on outdated systems to run their business. Integrating legacy systems with modern technology can improve efficiency, streamline processes, and save time and money. However, it’s important to approach the integration process carefully and methodically to ensure success.
Share on :
Keep On Reading
Subscribe to Our Newsletter
Subscribe to our weekly newsletters to get updates regarding our new production, behind the scene process of our art creation and much more.
After submitting this form you will receive an e-mail with a confirmation link that you must click to complete your request. Detailed information on processing and cancellation can be found in our privacy policy.