The Executive Guide to Reducing Downtime with AI and Predictive Analytics
Blog
4 Min 28 Sec Read
What’s the true cost of a machine suddenly stopping in a factory? Is it just a few minutes of lost production? No. Downtime doesn’t just pause your operations – it keeps on draining revenue, erode your organization’s efficiency, and chip your reputation away.
According to a report, even a small amount of downtime costs an average of $129 million each year for Fortune 500 Global manufacturers.
The good news is – AI can help you with it. They can make your organization produce faster, deliver faster, and reduce waste by an extent.
Predictive maintenance with AI can also assist you with analyzing machine data, detect early warning signs, and predict problems before they occur. But how do you use them? Let’s discuss.
Traditional vs. Predictive Maintenance – The Differences
Managing manufacturing equipment is quite like how we handle our car troubles.
Some people keep on waiting until their four-wheeler breaks down in the middle of the road, while others stay aware of the warning signs. The problem is – most people, including manufacturers, are always stuck in the first loop.
The Problem with Traditional Maintenance
Most factories usually depend on reactive maintenance – waiting for something to get damaged before fixing it. And it’s quite simple too, right? Why would you fix something that doesn’t require your attention yet? Well, considering how ruthless current manufacturing market has become, you certainly need to fix your tools before they break. Here’s why –
- Unpredictable Downtime: Machines can fail suddenly – which may stop your production unit entirely and lead to losses in revenue.
- Higher Expenses: Emergency fixes tend to cost more than planned maintenance, especially if you are outsourcing the technicians.
- Shorter Lifespan: Constant complete breakdowns of equipment can cause irreparable internal damage, which may wear them faster and shorten their lifespan.
So, to avoid these issues, using scheduled maintenance can be an ideal choice for your system. While this would require you to check and replace parts of a tool at set intervals, it would also be easier for you spot issues before they become more apparent.
However, this might not always be efficient for you as well. For example, in some cases, you may replace the parts too early, fearing for a breakdown, which may lead to wastage of money.
How Can Predictive Maintenance Help?
In predictive maintenance with AI, artificial intelligence focuses on analyzing real-time data from sensors, which helps them spot early signs of wear and tear. It can also help you with –
- Predicting failures before they happen and avoiding surprise breakdowns
- Fixing only what’s necessary while reducing labor or unnecessary part replacements
- Minimizing downtime and making sure that production is running smoothly
Thanks to predictive maintenance with AI, you can lower your maintenance-related expenses and ensure a longer machine life. It might also improve your organization’s production level and help you generate more revenue – as you can keep on running your factories without interruption.
How AI and Analytics Reduce Equipment Failures?
Machine, especially those used for manufacturing, generate a massive amount of data, including – temperature, pressure, vibration, etc.
Here are some technologies that helps with predictive maintenance –
- IoT Sensors: These are attached to machines & can help track performance in real-time.
- Machine Learning: AI and machine learning studies past failures of a machine to predict if and when it will break down again in the future.
- Data Analytics: It turns complex data into actionable insights to make it easier for you to understand where the problem lies and fix the same immediately.
There are quite a few industries that have been using predictive analytics to prevent machine failures already. Some of the examples of the same are as follows –
- Automotive: Car manufacturers can use AI and machine learning to track bot performance, which can help them avoid production halts effectively.
- Aerospace: Airlines monitor jet engines closely in real-time in order to prevent mid-air failures and avoid unfortunate accidents.
- Energy: Power plants use machine learning and artificial intelligence to maintain turbines to reduce blackouts and improve the efficiency of the machines.
MES and SCADA’s Role in Downtime Reduction
MES and SCADA usually work behind the scenes to ensure that machines, production schedules, and workers work in sync. So, let’s learn more about them.
MES and SCADA – A Brief Introduction
MES (also known as, Manfacturing Execution System) helps in tracking everything happening on the factory floor. It could include raw materials, final products, and the tools that are being used in the process. You can use it to optimize your workflows and spot inefficiencies accordingly.
SCADA (Supervisory Control and Data Acquisition), on the other hand, is a system that collects real-time data from machines and production lines. This can help you make decisions quicker.
Together, these two tools offer a clear view of what’s probably happening in production. However, they might get even more efficient if they’re being used with AI.
How Does AI Improve MES and SCADA
When AI for predictive maintenance and predictive analytics in manufacturing integrate with MES & SCADA – they can do much more than their usual doings. For example –
- AI can analyze SCADA data to detect early signs of equipment failure.
- By using MES, you can evaluate AI insights and adjust production schedules accordingly.
- MES and SCADA can help you fix issues before they can lead to a downtime.
The good thing is – your organization can experience a plethora of benefits by using predictive analysis in manufacturing. Here’s what you need to know about it –
- No more issues of unexpected shutdowns
- Machines can work at peak efficiency longer and more effectively
- Less wasted time can lead to fewer repairs, lesser expenses, and optimized maintenance
How Can INS3 Help You with Predictive Analysis?
When it comes to minimizing downtime in manufacturing, it’s always important to collaborate with an organization who has prior experience in this regard, like INS3.
Here’s how we can offer our assistance –
Comprehensive Data Infrastructure
With INS3, you can develop a robust data infrastructure by connecting machinery, collecting real-time data, and storing it securely. This foundation allows you to enable effective predictive analytics in manufacturing and implement proactive maintenance strategies to reduce –
- Equipment failures
- Associated downtime
MES Solutions and Manufacturing Intelligence
By integrating MES solutions, we can improve your operational efficiency through real-time equipment monitoring and control of production processes. These systems also offer valuable insights into equipment performance and enable timely maintenance to prevent potential problems.
SCADA & Data Modernization
Our team specializes in migrating or upgrading SCADA systems to modern architectures in order to improve process monitoring and data analysis capabilities. This modernization helps in reducing machine downtime in manufacturing by ensuring that the critical systems are operating efficiently.
The Bottom Line
Considering how fast-paced the manufacturing industry has become, it’s important to transition towards smart manufacturing and Industry 4.0 as soon as possible.
So, if there’s anything you need in that regard, INS3 is there for you. Give us a call to schedule a consultation session with our team today!
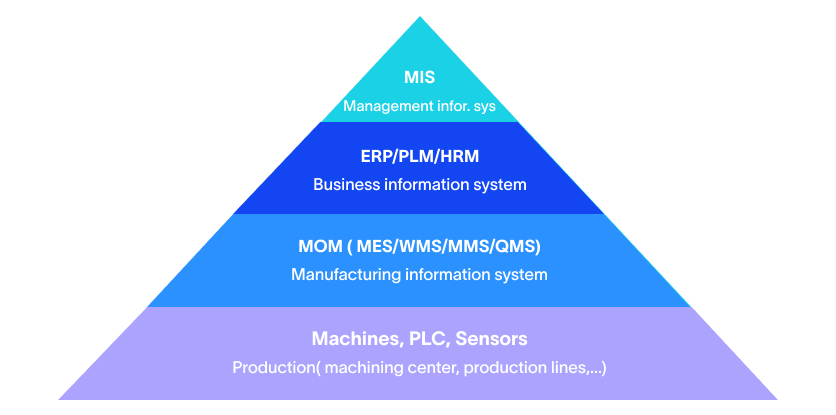
Agile MES: The Key to Unlocking Smart Manufacturing Success
MES is a computerized system used in manufacturing operations to track and document the transformation of raw materials into finished goods. An MES system typically manages and monitors work orders, equipment, materials, and personnel on the shop floor. The system provides real-time visibility into production processes, helps optimize manufacturing operations, and improves the overall efficiency of the manufacturing process.
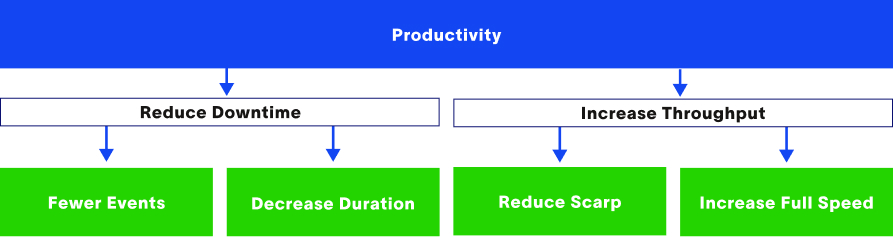
Understanding OEE: The Key to Manufacturing Efficiency
In today’s competitive manufacturing landscape, improving efficiency and productivity is crucial for businesses to remain competitive. One of the key metrics used to measure manufacturing efficiency is OEE or Overall Equipment Effectiveness. In this blog, we will take a closer look at OEE and its importance in manufacturing.
How to Effectively Conduct a Legacy System Integration
Legacy system integration can be a daunting task, but it’s a necessary one for many manufacturers that rely on outdated systems to run their business. Integrating legacy systems with modern technology can improve efficiency, streamline processes, and save time and money. However, it’s important to approach the integration process carefully and methodically to ensure success.
Share on :
Keep On Reading
Subscribe to Our Newsletter
Subscribe to our weekly newsletters to get updates regarding our new production, behind the scene process of our art creation and much more.
After submitting this form you will receive an e-mail with a confirmation link that you must click to complete your request. Detailed information on processing and cancellation can be found in our privacy policy.