Maximizing Manufacturing ROI with OEE and Expert System Integration
Blog
4 Min Read
In the dynamic landscape of manufacturing, maximizing efficiency is paramount for sustainable growth and competitiveness. Overall Equipment Effectiveness (OEE) has emerged as a crucial metric, offering a holistic assessment of production performance. However, to truly unlock the full potential of OEE and achieve a rapid return on investment (ROI), partnering with a knowledgeable system integrator like INS3 is essential. This collaboration ensures that the OEE system is not only effectively implemented but also seamlessly integrated into the existing manufacturing processes. Here’s how the combination of OEE and a system integrator like INS3 adds value across all project phases:
Understanding the numbers
- Conduct comprehensive needs analyses by engaging with various stakeholders to understand business goals and existing OT and IT landscapes.
- Facilitate clear communication among all parties, ensuring all expectations and concerns are addressed.
- Identify potential corner cases and unique scenarios that could impact the ROI.
- Leverage their technical expertise to design robust, scalable, and secure integration frameworks.
2. Design and Planning
- Evaluate current system for their Data Readiness
- Develop detailed integration architectures that align with business objectives.
- Design data flows that ensure seamless information exchange between systems.
- Plan for scalability and future adaptability to protect long-term investments.
3. Development and Testing
- Implement best agile practices in coding and configuration.
- Ensure proper data transformation and cleansing processes are in place.
- Integrate continuous testing into each sprint to ensure ongoing quality and rapid feedback.
- Identify and resolve potential issues before they impact the production environment.
4. Implementation
- Manage the rollout process, minimizing disruption to existing operations.
- Provide training and documentation to ensure smooth adoption by end-users.
- Implement real-time monitoring tools for proactive issue identification.
- Ensure all integrations are functioning as intended in the live environment.
5. Post-Implementation Support and Optimization
Post-implementation, continue to add value by:
- Providing ongoing support and troubleshooting.
- Analyzing system performance and suggesting optimizations.
- Adapting the integration as business needs evolve.
- Ensuring the integration continues to deliver value over time.
The Synergy of OEE
Combining the benefits of OEE with the expertise of INS3 creates a powerful synergy that maximizes ROI. OEE systems provide real-time visibility into manufacturing processes, enabling consistent production volumes, more efficient operations, reduced waste, and improved competitiveness. When these systems are implemented and integrated by experienced system integrators, the benefits are amplified:
- Enhanced Efficiency: Eensure that OEE systems are tailored to the specific needs of the organization, leading to more efficient manufacturing processes.
- Reduced Downtime: With real-time monitoring and predictive insights, integrators help minimize unplanned downtime and maintenance costs.
- Data-Driven Decisions: Lleverage advanced analytics to provide actionable insights, helping manufacturers make informed decisions that drive continuous improvement and cost savings.
- Scalability and Adaptability: Design OEE systems with scalability in mind, ensuring that the systems can evolve with the business and continue to deliver value over time.
Case Study: INS3’s Success in Achieving ROI
INS3 has a proven track record of helping manufacturers achieve significant ROI through the implementation of OEE and downtime and quality management solutions. For example, a mid-sized manufacturing client faced challenges with frequent machine downtime and inconsistent product quality. By partnering with INS3, they were able to:
- Identify Key Issues: INS3 conducted a thorough analysis of the client’s operations, identifying critical bottlenecks and inefficiencies.
- Implement Customized OEE Solutions: INS3 designed and implemented a tailored OEE system that provided real-time insights into machine performance, availability, and quality.
- Reduce Downtime: Through predictive maintenance and real-time monitoring, the client reduced unplanned downtime by 25%.
- Improve Product Quality: The OEE system enabled the client to identify and address quality issues promptly, resulting in a 15% reduction in defects.
- Achieve Rapid ROI: Within six months, the client saw a 20% increase in production efficiency and a substantial improvement in overall profitability.
Not All OEE Implementations Are Created Equal
It’s important to note that not all OEE implementations are created equal. The success of an OEE system depends on various factors, including the accuracy of data collection, the relevance of the metrics used, and the ability to interpret and act on the data. INS3’s experience and expertise ensure that OEE systems are customized to meet the unique needs of each client, maximizing their potential for ROI.
- Customized Solutions: INS3 tailors OEE systems to the specific requirements of each client, ensuring that the metrics used are relevant and actionable.
- Accurate Data Collection: INS3 employs advanced technologies to ensure accurate and reliable data collection, eliminating the inconsistencies that can arise from manual data entry.
- Actionable Insights: INS3 provides clients with the tools and knowledge needed to interpret OEE data effectively and implement continuous improvement initiatives.
By partnering with INS3, manufacturers can ensure that their OEE systems are not only effectively implemented but also optimized for maximum impact. This strategic approach leads to significant improvements in productivity, quality, and cost efficiency, resulting in a swift and substantial return on investment.
Get in touch to start your Digital Transformation Journey.
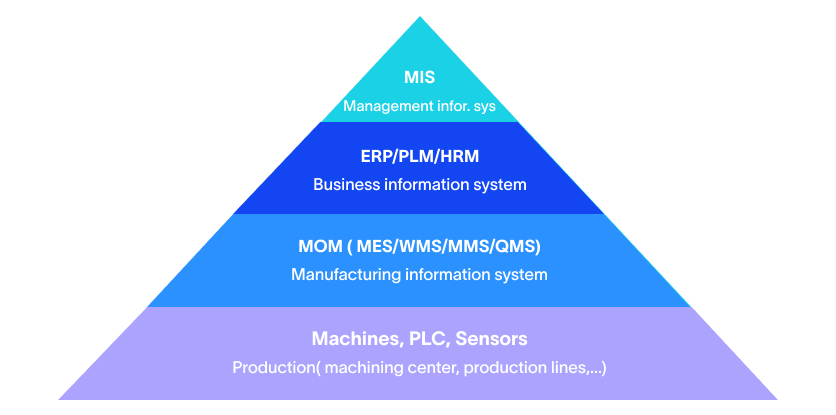
Agile MES: The Key to Unlocking Smart Manufacturing Success
MES is a computerized system used in manufacturing operations to track and document the transformation of raw materials into finished goods. An MES system typically manages and monitors work orders, equipment, materials, and personnel on the shop floor. The system provides real-time visibility into production processes, helps optimize manufacturing operations, and improves the overall efficiency of the manufacturing process.
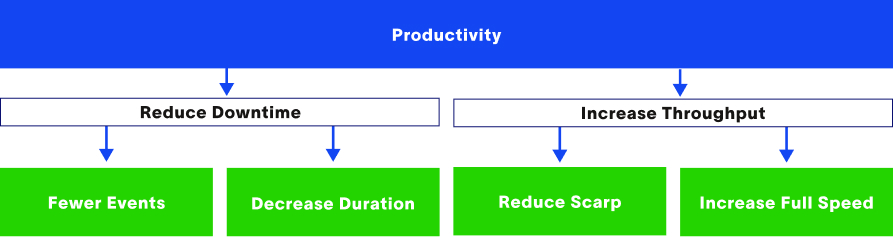
Understanding OEE: The Key to Manufacturing Efficiency
In today’s competitive manufacturing landscape, improving efficiency and productivity is crucial for businesses to remain competitive. One of the key metrics used to measure manufacturing efficiency is OEE or Overall Equipment Effectiveness. In this blog, we will take a closer look at OEE and its importance in manufacturing.
How to Effectively Conduct a Legacy System Integration
Legacy system integration can be a daunting task, but it’s a necessary one for many manufacturers that rely on outdated systems to run their business. Integrating legacy systems with modern technology can improve efficiency, streamline processes, and save time and money. However, it’s important to approach the integration process carefully and methodically to ensure success.
Share on :
Keep On Reading
Subscribe to Our Newsletter
Subscribe to our weekly newsletters to get updates regarding our new production, behind the scene process of our art creation and much more.
After submitting this form you will receive an e-mail with a confirmation link that you must click to complete your request. Detailed information on processing and cancellation can be found in our privacy policy.