From Data to Decisions: How Operations Managers Can Leverage Manufacturing Analytics
Blog
6 Min Read
While manufacturing systems cannot communicate their inefficiencies directly, they still provide signals to us – through data. However, the challenge lies in how we interpret it in order to –
- Predict equipment failures
- Find out inefficiencies
- Optimize processes
This is where manufacturing analytics becomes indispensable. For example, you can use big data to avoid making reactive decisions and adopt a more data-driven, proactive approach. Besides, it can also play an important role in Industry 4.0 by integrating AI and IoT in your system.
By evaluating real-time data, you can predict potential disruptions even before they offer, improve your organizational productivity, and optimize resource allocations accordingly.
However, if you’re new to manufacturing analytics, you’re probably here to get some fundamental information about it before diving too deep. So, let’s discuss that, first.
Manufacturing Analytics – Types and Benefits
Manufacturing analytics, in essence, focuses on collecting, analyzing, and interpreting data related to manufacturing operations. While it’s usually used to improve and optimize the physical production processes, you can also implement it for inventory management, procurement, and sales.
Types of Analytics
Manufacturing operations analytics can be categorized into four different classes, including –
- Descriptive: It works on what has happened in the past by evaluating historical data of your equipment. This, in turn, can help you identify trends and performance metrics accordingly.
- Diagnostic: With this type of analytics, you can investigate why certain events are occurring in your organization by examining different historical patterns.
- Predictive: This uses statistical algorithms and machine learning to forecast future trends. However, these are usually based on historical data, so you cannot solely depend on it.
- Prescriptive: Prescriptive analytics suggests different types of actions to optimize outcomes based on the predictive insights you have received.
Benefits of Manufacturing Analytics
There are quite a few benefits of manufacturing analytics that go under the radar, considering how less people use this technique in their organization. So, let’s talk about it.
Learn how AI-driven predictive maintenance can help reduce downtime and improve operational efficiency.
Improved Efficiency
Manufacturing plants usually generate a massive amount of data every day. However, raw information isn’t really useful for anyone. So, if you want to make sense of it, you’ll have to use analytics to track performance, spot bottlenecks, and make quick adjustments – all in real-time. This will lead to less waste, fewer delays, and much better results.
Better Product Quality
Quality control isn’t just about spotting defects in your products anymore. It’s more about how well you can prevent them. Predictive analytics in manufacturing can detect patterns that may lead to flaws and notify you about the same at the earliest. Furthermore, you can also use it to analyze sensor data to adjust the processes accordingly to prevent the defects from happening.
Cost Reduction
With analytics, you can find cost-saving opportunities with just a single click. These may include –
- Reducing energy usage
- Optimizing labor to take care of the health of your workers
- Automating repetitive tasks to save even more time and energy
This can result in higher customer satisfaction and fewer recalls of your products. In hindsight, this can also be beneficial for maintaining or improving your reputation.
Predictive Maintenance
Unexpected equipment failures can slow down production and drive-up repair costs. So, instead of waiting for your equipment to break, predictive maintenance uses AI and analytics to monitor machine health. This way, it becomes easier for you to schedule routine maintenance for each tool perfectly without investing resources unnecessarily.
How Operations Managers Can Use Manufacturing Analytics?
There was a time when manufacturing was just about machines and assembly lines. However, now, it’s become all about data. So, if you are an operations manager, you have to know how to use this information in order to run your operation more profitably.
Align with Company Objectives
Every company has its own goals – cutting costs, improving product quality, boosting efficiency, etc. For example, if you want to reduce waste, it might be better to track your material usage and check where your resources are being used. On the other hand, if your aim is to improve the production cycle, you can analyze your workflow data and assess your efficiency accordingly.
Data-Driven Decision Making
Data-driven decision making in manufacturing means looking at real numbers produced by your organization before making a call. For example, if you think your company needs to invest in a new machine, it might be better to use predictive analytics to check –
- How many manual tasks are being performed currently
- Is there any kind of bottlenecks happening due to having less machinery or not
Stakeholder Analysis
Analytics doesn’t just help managers – it benefits everyone in the organization as well. For example, if executives are looking for insights on costs and revenue, they can get that in one click. Frontline workers, on the other hand, can use analytics for real-time troubleshooting to make sure that there are no bottlenecks occurring during their work.
INS3’s Role in Implementing Manufacturing Analytics
Making sense of manufacturing data can, sometimes, feel overwhelming. After all, you are dealing with too many systems and data without enough clarity. So, that’s where we can offer our assistance. Here’s how we can do it –
Unified Namespace
One of the biggest challenges in manufacturing has always been the effort of getting different systems to work collaboratively. In order to solve this, our team uses a UNS (Unified Namespace) approach, which aligns with ISA95 standards, to create a seamless data flow. Instead of scattered insights, we can offer a centralized hub of real-time information. It, in turn, can help you make more accurate data-driven decision making in manufacturing.
Customized Solutions
Every factory is different and has a unique method or routine for working. That’s why we don’t create or work with a single strategy. Whether it’s predictive maintenance, production optimization, or quality control – we can make sure that your data works for you, not the other way around.
Data Readiness Assessment
Not all data is going to be useful for your organizational aim.
So, before we start working on a fix, our team focuses on finding the right kind of information by using Data Readiness Assessment and evaluating the same first. This can you find the data you need and start working on the improvements right away.
The Final Say
At the end of the day, our goal is simple – turning your manufacturing data into better business outcomes. However, if all you need is someone who can direct and guide you regarding manufacturing analytics properly, we can help you with that as well. Just let us know what you need, and we’ll try our best to offer insights or assistance on the same.
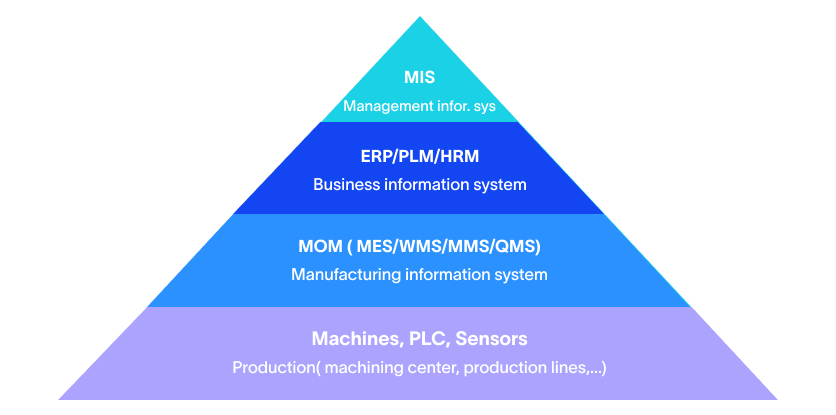
Agile MES: The Key to Unlocking Smart Manufacturing Success
MES is a computerized system used in manufacturing operations to track and document the transformation of raw materials into finished goods. An MES system typically manages and monitors work orders, equipment, materials, and personnel on the shop floor. The system provides real-time visibility into production processes, helps optimize manufacturing operations, and improves the overall efficiency of the manufacturing process.
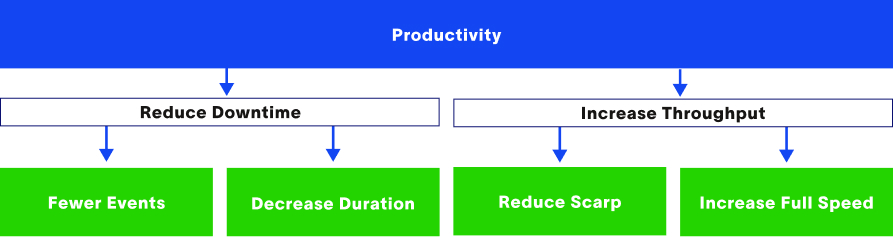
Understanding OEE: The Key to Manufacturing Efficiency
In today’s competitive manufacturing landscape, improving efficiency and productivity is crucial for businesses to remain competitive. One of the key metrics used to measure manufacturing efficiency is OEE or Overall Equipment Effectiveness. In this blog, we will take a closer look at OEE and its importance in manufacturing.
How to Effectively Conduct a Legacy System Integration
Legacy system integration can be a daunting task, but it’s a necessary one for many manufacturers that rely on outdated systems to run their business. Integrating legacy systems with modern technology can improve efficiency, streamline processes, and save time and money. However, it’s important to approach the integration process carefully and methodically to ensure success.
Share on :
Keep On Reading
Subscribe to Our Newsletter
Subscribe to our weekly newsletters to get updates regarding our new production, behind the scene process of our art creation and much more.
After submitting this form you will receive an e-mail with a confirmation link that you must click to complete your request. Detailed information on processing and cancellation can be found in our privacy policy.