The Digital Transformation Roadmap for Manufacturing Executives
Blog
3 Min 40 Sec Read
Considering how quickly the modern manufacturing scene has evolved, you simply cannot stick to the old-school methods anymore. So, the solution here could be to move away from the traditional ecosystem and transform your organization digitally.
But the thing is – digital transformation isn’t just about buying new technology and integrating it in your system. It’s about having a smart manufacturing strategy that connects systems, streamlines operations, and helps you make better decisions.
And for manufacturing executives, the challenge isn’t about knowing what to adopt. Instead, you have to understand how you can make it work. So, in this article, we are going to break down the key steps of a digital transformation roadmap & make sure that you’re moving forward confidently.
Let’s begin.
Assessing Your Current Manufacturing Technology Stack
Before you jump into digital transformation in manufacturing, it’s important to understand where you are standing right now. In this aspect, you can start by looking at your current technology stack. And once you’re done with it, try to find what systems are in place, identify bottlenecks, etc.
Here are some questions you need to find answers to as well –
- Are you using automation and smart sensors in your machinery effectively?
- Is there any real-time access to data available in your project or are you still relying on manual reports?
- How well are your current systems integrated with newer technologies?
Remember, this self-check is going to lay the foundation for industry 4.0 digital transformation. So, once you know what’s working and what’s not working for you, you can start making smarter decisions about what you should replace, upgrade, or integrate.
Your Blueprint for Digital Transformation – Explore the essential steps to building a connected, data-driven smart factory. Read our executive guide now!
Identifying Key Areas for Improvement
Once you have assessed your current setup, the next step in digital transformation in manufacturing will be figuring out where to improve. Remember, not every system requires an overhaul. Some will probably need better integration, while others might be outdated and hold you back.
Some key areas to focus on can include –
- MES (Manufacturing Execution Systems): It helps in tracking and managing production in real time and reduces waste significantly. You can also use this tool to ensure better coordination between people and machines.
- SCADA (Supervisory Control and Data Acquisition): It monitors and controls industrial processes while offering centralized data visualization for the users. SCADA is also crucial for industries who require strict process control.
- IIoT (Industrial Internet of Things): It connects machines and devices to make operations smoother. You can also use it for remote monitoring and predictive maintenance. Also, IIoT can reduce downtime by detecting issues before they even happen.
- AI and Machine Learning: With AI and ML, you can analyze a large amount of data to find patterns and improve automation & decision-making. These technologies can also be used to predict demand, optimize schedules, and reduce errors.
- Advanced Analytics: Advanced analytics can turn raw data into actionable insights and help in tracking performance, spotting inefficiencies, and planning ahead. Finally, it will also support data-driven decision-making for continuous improvement.
Developing a Phased Digital Transformation Strategy
If you are trying initiate a project of digital transformation in manufacturing, you’ll need a full-proof plan first. Here’s how you may structure it –
- Start Small: You should start your journey by making low-risk, high-impact changes. For example, instead of replacing a system, you can try upgrading it or automate a task or two. We’d also suggest testing out IIoT in manufacturing by connecting a few key machines to monitor their performance and check if there’s any change needed or not.
- Scale Up Gradually: If you have created plans for pilot projects, try to expand them to the other areas. You may also try improving data collection and analytics for better decision-making and integrating systems like manufacturing digitalization platforms to connect different processes together.
- Optimize for Long-Term Success: Finally, once you are done with the previous steps, you can focus on predictive maintenance and AI-driven automation. Investing in cybersecurity to protect digital assets and training employees for the transformation process accordingly.
Building the Business Case for Investment
Digital transformation isn’t just about upgrading your technologies. It’s also about proving that the investment makes sense, in terms of your budget and the organization’s long-term success. Before moving forward with your plan, you’ll require a strong business case – one that shows clear ROI and cost savings. Here are some tips on how you can do it –
- Predictive maintenance (driven by AI and machine learning in manufacturing) can help you catch issues with your manufacturing platform before they cause breakdowns.
- Automation in manufacturing can reduce repetitive tasks, which may allow workers to focus on high-value jobs and complete them accordingly.
- Smart systems can help in cutting waste and expenses, optimizing production, and improving energy usage throughout the entire organization.
Apart from this, you’ll also need to calculate your ROI effectively. Here’s how you can do it –
- Hardware, software, training, and implementation-related expenses
- Increased production, improved quality, and reduced waste
- Tracking KPIs (key performance indicators) to see the real impact
Finally, as you are building a business case, it’s important to remember that executives will want to see the numbers. If you can showcase how digital performance in manufacturing will boost efficiency, cut costs, and improve your overall productivity.
Finding the Right Technology Partners
Although it may sound dreamy, digital transformation in manufacturing is a lengthy and difficult journey. So, you’ll need the right partner to be with you and offer you the right direction altogether. Here’s how we, at INS3, can offer our assistance in this regard –
- Connecting legacy systems with newer technologies
- Implementing real-time data analytics to improve efficiency
- Developing step-by-step strategies to reduce risk and maximize ROI
Conclusion
Finding the right technology partner makes digital transformation easier and more effective. With a company like INS3, manufacturers can confidently adopt new technologies without disrupting operations. So, if there’s anything you need from us, don’t forget to give us a call.
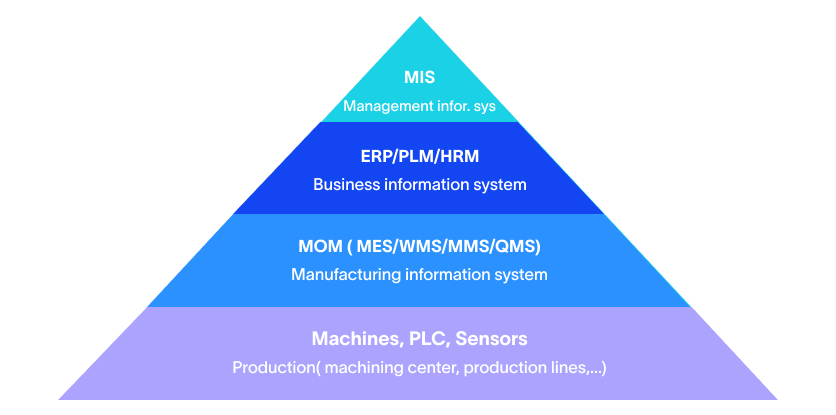
Agile MES: The Key to Unlocking Smart Manufacturing Success
MES is a computerized system used in manufacturing operations to track and document the transformation of raw materials into finished goods. An MES system typically manages and monitors work orders, equipment, materials, and personnel on the shop floor. The system provides real-time visibility into production processes, helps optimize manufacturing operations, and improves the overall efficiency of the manufacturing process.
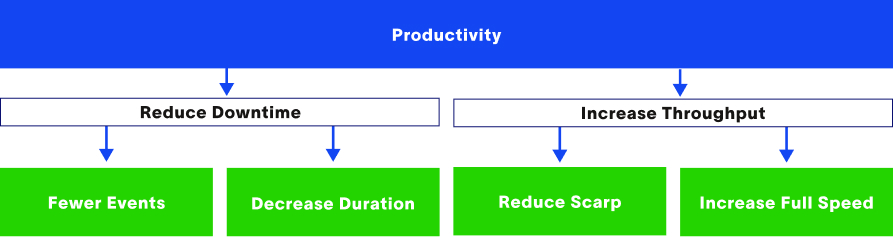
Understanding OEE: The Key to Manufacturing Efficiency
In today’s competitive manufacturing landscape, improving efficiency and productivity is crucial for businesses to remain competitive. One of the key metrics used to measure manufacturing efficiency is OEE or Overall Equipment Effectiveness. In this blog, we will take a closer look at OEE and its importance in manufacturing.
How to Effectively Conduct a Legacy System Integration
Legacy system integration can be a daunting task, but it’s a necessary one for many manufacturers that rely on outdated systems to run their business. Integrating legacy systems with modern technology can improve efficiency, streamline processes, and save time and money. However, it’s important to approach the integration process carefully and methodically to ensure success.
Share on :
Keep On Reading
Subscribe to Our Newsletter
Subscribe to our weekly newsletters to get updates regarding our new production, behind the scene process of our art creation and much more.
After submitting this form you will receive an e-mail with a confirmation link that you must click to complete your request. Detailed information on processing and cancellation can be found in our privacy policy.