Legacy System Integration: Best Practices and Strategies
Blog
4 Min Read
Legacy system integration can be a daunting task, but it’s a necessary one for many manufacturers that rely on outdated systems to run their business. Integrating legacy systems with modern technology can improve efficiency, streamline processes, and save time and money. However, it’s important to approach the integration process carefully and methodically to ensure success.
What Is Legacy Systems Integration?
Legacy systems integration is the process of connecting or merging an existing software or hardware system with a new or upgraded system. In many cases, organizations may have invested heavily in legacy systems that have been in place for many years and continue to be critical to their business operations. However, these systems may have limitations, such as outdated technology, lack of interoperability with newer systems, or difficulty in maintaining and supporting them.
Legacy system integration involves the design and implementation of a solution that allows these legacy systems to work with newer technologies and systems, providing the necessary data and functionality to meet the needs of the business. By integrating legacy systems with newer technologies, organizations can extend the life of their legacy systems, while taking advantage of new capabilities and functionality that can improve business operations and performance.
Effective legacy system integration requires careful planning and execution, including a thorough assessment of the current legacy systems, identification of integration requirements and goals, and a well-designed integration strategy. The integration process should be designed to minimize disruption to existing systems and operations, while ensuring that the new system meets the needs of the business and users.
What are the types of legacy systems integrations?
There are several types of legacy systems integration, and the specific approach depends on the unique needs and circumstances of each organization. Here are some of the most common types of integration:
- Middleware Integration
Middleware integration involves using middleware software to integrate legacy systems with newer technologies. Middleware acts as a bridge between different systems, enabling them to communicate and exchange data. This can include software such as message queues, application servers, and service-oriented architectures (SOA). - System-level Integration
System-level integration is the process of connecting different systems at a low-level, often at the hardware or operating system level. This type of integration enables legacy systems to work together seamlessly with newer systems, sharing resources and exchanging data. This approach can be particularly useful for organizations that have invested heavily in legacy systems and want to extend their useful life, without the need for a complete replacement. - Process Integration
Process integration involves connecting different business processes and workflows across various systems to create a unified and streamlined process. This type of integration helps organizations to reduce errors, increase efficiency, and improve overall business performance. For example, a legacy system might have a separate process for inventory management, while a newer system might handle order processing. By integrating these systems at the process level, businesses can automate the flow of data between them, allowing for real-time visibility into inventory levels and order processing. This integration can also help businesses optimize their supply chain management, reduce lead times, and improve customer satisfaction. - Cloud Integration
Process integration is a type of legacy system integration that involves connecting different systems to support end-to-end business processes. This enables organizations to streamline their operations and improve efficiency by eliminating manual tasks and reducing errors. Process integration can involve integrating multiple systems such as Enterprise Resource Planning (ERP), Customer Relationship Management (CRM), Supply Chain Management (SCM), and other legacy systems. By integrating these systems, organizations can optimize their business processes and reduce the time and effort required to complete tasks, resulting in improved productivity and reduced costs.
Each type of integration has its own benefits and challenges, and the choice of approach will depend on factors such as the specific systems involved, the business needs, and the available resources. It is important to carefully evaluate each option to determine the best approach for achieving the desired integration goals.
What are the steps you can take to effectively conduct a legacy system integration?
Legacy systems integration is the process of connecting or merging an existing software or hardware system with a new or upgraded system. In many cases, organizations may have invested heavily in legacy systems that have been in place for many years and continue to be critical to their business operations. However, these systems may have limitations, such as outdated technology, lack of interoperability with newer systems, or difficulty in maintaining and supporting them.
Assess your current systems
The first step in any legacy system integration project is to assess your current systems. This includes understanding what data your legacy systems are storing, how they are structured, and how they interact with other systems. You should also identify any inefficiencies or pain points in your current processes that can be addressed through integration.
Identify integration requirements
Once you have a clear understanding of your current systems, you can start to identify the requirements for the integration project. This includes determining what data needs to be migrated, what systems need to be integrated, and what functionality is required.
Better decision-making
Industry 4.0 technologies provide businesses with real-time data and analytics, enabling them to make better decisions. This helps businesses identify and solve problems quickly, improve processes, and respond to changing market conditions.
Develop a plan
With your integration requirements identified, it’s time to develop a plan for the integration project. This plan should include a timeline, a list of milestones, and a budget. You should also identify any potential risks or roadblocks that could impact the project and develop contingency plans.
Choose the right integration approach
There are a few different approaches you can take when integrating legacy systems with modern technology. These include:
Replacing the legacy system with a new, modern system.
Building a custom integration solution Using an off-the-shelf integration solution
Sustainable practices
Industry 4.0 technologies can help businesses reduce their environmental impact. For example, by using predictive maintenance to reduce equipment downtime, businesses can reduce energy consumption and greenhouse gas emissions.
In conclusion, legacy system integration can be a complex process, but it’s an important one for companies that want to modernize their operations. By following the steps outlined above, you can effectively conduct a legacy system integration project that improves efficiency, streamlines processes, and saves time and money.
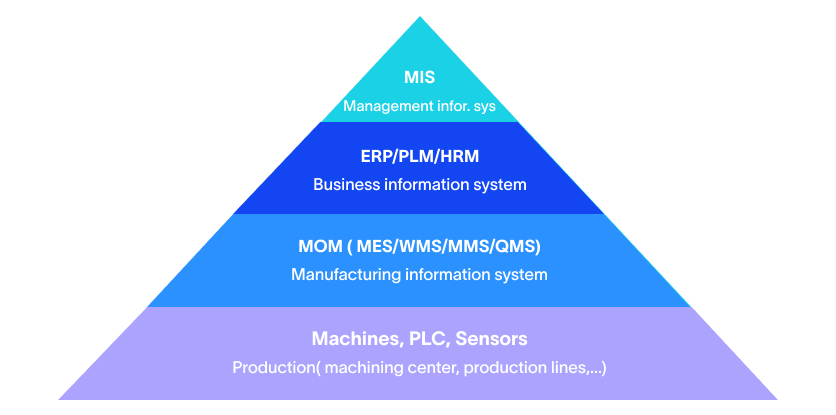
Agile MES: The Key to Unlocking Smart Manufacturing Success
MES is a computerized system used in manufacturing operations to track and document the transformation of raw materials into finished goods. An MES system typically manages and monitors work orders, equipment, materials, and personnel on the shop floor. The system provides real-time visibility into production processes, helps optimize manufacturing operations, and improves the overall efficiency of the manufacturing process.
Understanding OEE: The Key to Manufacturing Efficiency
In today’s competitive manufacturing landscape, improving efficiency and productivity is crucial for businesses to remain competitive. One of the key metrics used to measure manufacturing efficiency is OEE or Overall Equipment Effectiveness. In this blog, we will take a closer look at OEE and its importance in manufacturing.
How to Effectively Conduct a Legacy System Integration
Legacy system integration can be a daunting task, but it’s a necessary one for many manufacturers that rely on outdated systems to run their business. Integrating legacy systems with modern technology can improve efficiency, streamline processes, and save time and money. However, it’s important to approach the integration process carefully and methodically to ensure success.
Share on :
Keep On Reading
Subscribe to Our Newsletter
Subscribe to our weekly newsletters to get updates regarding our new production, behind the scene process of our art creation and much more.
After submitting this form you will receive an e-mail with a confirmation link that you must click to complete your request. Detailed information on processing and cancellation can be found in our privacy policy.