How Data Analytics Reduces Downtime in Manufacturing
Blog
7 Min 23 Sec Read
Data analytics in manufacturing has completely reshaped how companies tackle the issue of downtime. Instead of just reacting to breakdowns, manufacturers now track both planned and unplanned interruptions in detail. This, in turn, helps them find hidden patterns, which are related to the breakdowns, through proper analytics.
And the good news is, this shift isn’t just keeping the machines running all the time. It’s also helped reduce downtime in manufacturing, cut maintenance costs, and avoid disruptions.
Thanks to predictive maintenance, you can also spot issues before they cause failures and fix them at the right time. This doesn’t just boost the uptime of your business; it also leads to better product quality and smoother workflows. In a competitive market where every second counts, using data analytics in manufacturing is one of the smartest ways to gain an edge.
Capturing the Full Downtime Picture
The process of reducing downtime in manufacturing begins with a complete and precise understanding of when, why, and how production stops. That means going beyond just logging machine failures – like, getting a holistic view of both planned and unplanned downtime, enriched with real-time data monitoring and human insights.
Let’s learn more about it.
Unplanned Downtime Events
Unplanned stoppages can range from full-scale system failures to momentary hiccups that can add up to major inefficiencies over time. Here’s what it may include –
- Major equipment failures that may bring production to a standstill
- Operational interruptions, like jams that need manual intervention
- Quality-related halts, where faulty products require inspection or rejection
- Micro stops, split-second interruptions that seem insignificant at first but can erode your machinery’s capacity by 10% to 15%
Factory automation plays a critical role in tracking these events with precision. Integrated systems capture every detail closely and timestamp each event down to the millisecond & classify disruptions automatically while storing contextual process data.
Planned Downtime Activities
Planned downtime is important for every manufacturing business. But that doesn’t mean you can’t optimize it. A massive share of non-productive time comes from –
- Routine maintenance and inspections
- Product changeovers and associated setup adjustments
- Cleaning, sanitation, and calibration procedures
- Tooling replacements and fine-tuning
Traditionally speaking, planned downtime hasn’t been properly scrutinized as closely as breakdowns. However, through proper analytical rigor, you can refine these necessary activities and make them faster and more efficient without compromising quality.
Contextual Operator Input
Machines can record the time they weren’t able to work for, but only humans can explain the reason behind it. Operators provide critical insights that turn raw data into actionable insights. Here’s what modern systems incorporate to bridge the gap between real-world context and automation –
- Mobile-friendly interfaces for immediate reason-code entry
- Tailored downtime hierarchies that align with specific production processes
- Video and photo documentation to capture visible issues in real time
- Standardized reporting for consistency in downtime classification
By integrating IoT in manufacturing with human expertise, you can get a deeper understanding of downtime causes conclusively.
Maintenance Data and Historical Analysis
Comprehensive downtime analysis won’t be completed if you don’t link the stoppage times with maintenance activities. A well-structured approach for this includes –
- Information on maintenance interventions associated with specific equipment and related components
- Understanding failure patterns and replacement histories of critical parts
- Going through technician reports detailing resolution steps and observed issues
- Learning MTBF (Mean Time Between Failures)
When real-time data monitoring is combined with historical insights, you can refine your maintenance strategies to –
- Extend equipment lifespan
- Improve their reliability
- Prevent future disruptions
In the long run, you can use a data-driven approach to ensure that every intervention (reactive or preventive) contributes to a more resilient and efficient production system.
Analytics Approaches That Deliver Measurable Impact
Once you have implemented a solid data collection system in place, you can start using that data to make correct downtime-related predictions. For example, targeted analytics can help you identify hidden inefficiencies, drive smarter decisions, & reduce downtime in manufacturing. Here’s what you need to know about it –
Pattern Recognition
Collecting raw data isn’t going to be enough. You’ll also need the right analytics to spot patterns and uncover the real reasons behind downtime. Here’s how you can do it –
- Pareto analysis to find out the most frequent and costly downtime sources
- Correlation mapping between production variables and stoppage trends
- Sequence analysis to identify cascading failures and triggering events
- Multi-factor root cause analysis to eliminate recurring breakdowns
- Shift-to-shift and product-to-product comparisons to expose inconsistencies
Instead of reacting to issues as they pop up, you can use these insights to fix the root causes and reduce long-term downtime-related issues.
Predictive Analytics and Early Warnings
Advanced predictive analytics and AI-driven monitoring can detect problems long before they turn into failures. By identifying subtle deviations in machine behavior, manufacturers can present breakdowns instead of scrambling to fix them.
Some of the key capabilities can include –
- Anomaly detection to flag unusual patterns in real-time
- Risk assessment tools to prepare for potential disruptions in production
- Failure forecasting models that predict breakdown risks ahead of time
- Early warning systems that alert teams to developing conditions
- Prescriptive maintenance recommendations that optimize repair schedules
With these AI-driven downtime reduction strategies, you can shift your maintenance duties from being reactive to proactive. This, in turn, can help your business increase its production efficiency and reduce unnecessary expenses.
Explore proven strategies top leaders use to reduce downtime with AI and predictive analytics in this must-read executive guide.
Optimizing Planned Downtime
Unplanned failures aren’t the only cause of lost production time. Changeovers and planned maintenance, if you are not optimizing them, can also affect your output. This is why manufacturing process optimization is so important –
- Condition-based maintenance schedules to reduce unnecessary servicing
- Comparative analysis to identify the best practices from high-performing shifts
- Sequencing algorithms that minimize setup time between product runs
- Standard work development to streamline maintenance procedures
By using data-driven improvements, you can reduce planned downtime by 20% to 30% – while improving production quality even more.
Case Study: Food & Beverage Manufacturer
A major food and beverage producer turned to advanced downtime analytics to tackle inefficiencies in their packaging operations. The results were striker to say the least.
In just four months, they experienced a significant growth in production while reducing downtime massively. Here’s what they achieved –
- Pinpointing a Hidden Bottleneck: A micro stop pattern, which was appearing on their primary filling line 120+ times daily, was found out and addressed.
- Reducing Changeover Time by 28%: By applying SMED principles and analyzing downtime data, they could streamline product switches easily.
- Uncovering Material-Related Stoppages: Machine learning for manufacturing helped detect a correlation between specific raw material batches & failure rates.
- Improving Overall Equipment Availability: These improvements led to substantial annual savings and higher production efficiency.
Their success wasn’t just related to collecting. It was also about using the right tools to find a meaning from it. Factory automation, powered by MES solutions and SCADA systems, allowed for real-time tracking. Predictive analysis, on the other hand, revealed inefficiencies that manual monitoring could’ve missed.
Best Practices for Successful Implementation
Manufacturers that have successfully reduced downtime in manufacturing through data analytics follow a few important strategies. Here’s what it may include –
Defining Clear Goals from the Beginning
If you don’t have a clear targe in front of you, even the best downtime reduction strategies can fall short. So, before you dive into analytics, it’ll be important to –
- Set specific downtime reduction objectives
- Establish a set of baseline performance metrics for comparison
- Choose relevant KPIs like OEE, MTBF, and MTTR
- Set realistic and manageable improvement timelines
Focus on Data Quality & Accuracy
Bad data leads to bad decisions. So, in order to make business intelligence in manufacturing effective, you have to ensure that whatever data you’re collecting is reliable and complete. Here are some ways to do it –
- Strengthen direct connectivity to control systems and IoT devices
- Make operator input easier with user-friendly dashboards
- Standardize downtime reason codes for consistency
- Cross-check information with real-world production conditions
Get Everyone Involved in It
A successful data-driven strategy should never depend on analytics. It should also focus on the people who are using the machinery and partaking in the production process daily. Here’s how you can collect information from them as well –
- Bring engineering, maintenance, and operations teams together
- Involve shop floor workers in system design, as they know the machines best
- Provide hands-on training to ensure adoption
- Set up proper feedback loops to refine and improve processes over time
Take It One Step at a Time
Don’t try to fix everything at once. The best way to implement predictive analytics and downtime reduction strategies is through gradual, well-tested steps.
Here’s what it can include –
- Start with high-impact, well-understood equipment
- Validate insights with small pilot projects before scaling
- Apply different but successful strategies to similar equipment
- Expand implementation only after measurable improvements are proven
Why INS3 is the Right Partner for Downtime Reduction?
Tracking downtime isn’t just about having the right information. It’s also about knowing what you need to do – and that’s where INS3 shines brightly. With years of expertise in manufacturing process optimization, cutting-edge predictive analytics, and a hands-on approach, we’ve helped manufacturers across industries effectively.
Here’s how we can help you out –
Deep Expertise in Factory Systems Integration
Our team just doesn’t collect data – we make it work for you. Our team specializes in seamlessly integrating factory automation systems to ensure that every piece of data is captured and turned into actionable insights. Our expertise includes –
- Direct PLC integration across Allen-Bradley, Siemens, GE, and more
- SCADA system integration with platforms like Ignition, GE Digital & Tatsoft
- MES solutions that link shop floor data to production management
- Time-series historian deployment for high-end data storage
- Advanced analytics platforms that transform raw data into business insights
A Proven Downtime Reduction Strategy
At INS3, we don’t believe in guesswork. Our team follows a structured, results-driven approach to downtime reduction strategies, which have been refined through years of successful implementation. Here’s what it includes –
- Comprehensive Performance Assessments: We will evaluate your current downtime landscape to identify high-impact opportunities at the beginning.
- Smart System Architecture Design: Then, our team will focus on the state of your equipment and make sure that it’s tracked properly.
- Seamless Implementation: Our implementation process is perfectly designed to improve production efficiency without disrupting operations.
- Data Validation & Accuracy Checks: Unreliable data usually leads to making unreliable decisions. So, after collecting information, we always check closely how accurate and usable they are for our purpose.
- Actionable Analytics Frameworks: In this stage, we will highlight the most critical areas to make immediate improvements.
- Ongoing Support for Continuous Improvement: Reducing downtime isn’t a one-time fix, it’s an evolving strategy. So, we will offer our support until the entire process (which we implemented) gets normalized into your system.
Industry-Wide Experience and Tailored Solutions
Every industry has its own set of downtime challenges. With extensive experience across multiple manufacturing environments, INS3 brings cross-industry insights to solve even the toughest operational bottlenecks –
- Food & Beverage: Strict cleaning and sanitation requirements
- Pharmaceuticals: Regulatory compliance and batch traceability
- Discrete Manufacturing: Complex material flow and assembly processes
- Continuous Process Industries: High reliability demands and predictive maintenance
By using our broad experience, we can apply proven best practices from one sector to another and improve results accordingly.
Beyond Just Technology – A Long-Term Partnership
At INS3, we believe business intelligence in manufacturing isn’t just about technology. It’s about empowering people in your organization. That’s why we go beyond the process of implementation to make sure that your team is set up for long-term success.
- Knowledge Transfer: Building internal expertise so you can sustain improvements independently, whenever it’s needed.
- Continuous Analytics Support: Helping you refine your downtime reduction approach over time – as long as you need us there.
- Regular Performance Reviews: Identifying new opportunities for improvement as operations keep evolving.
- Ongoing Training: Keeping new and existing employees up to speed.
- Future-Ready Roadmaps: Guiding you toward the next phase of manufacturing process optimization.
With INS3, you’re not just adopting a predictive analytics solution, you’re gaining a partner committed to helping you reduce downtime in manufacturing and drive lasting efficiency. Let’s transform equipment availability into a competitive advantage!
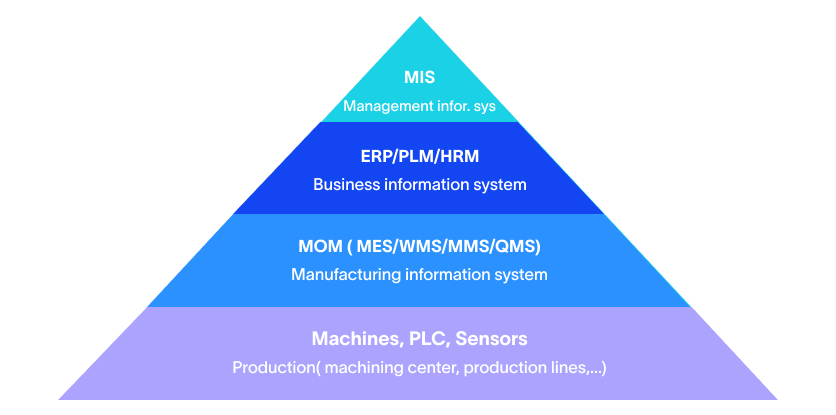
Agile MES: The Key to Unlocking Smart Manufacturing Success
MES is a computerized system used in manufacturing operations to track and document the transformation of raw materials into finished goods. An MES system typically manages and monitors work orders, equipment, materials, and personnel on the shop floor. The system provides real-time visibility into production processes, helps optimize manufacturing operations, and improves the overall efficiency of the manufacturing process.
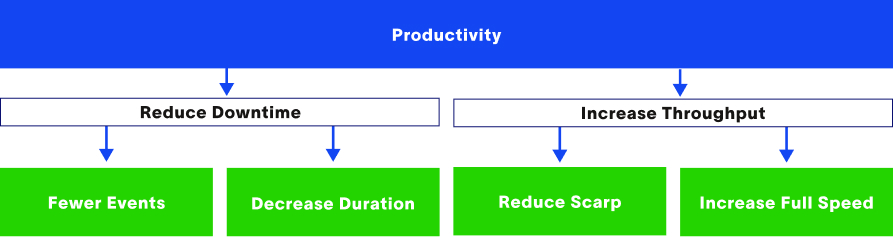
Understanding OEE: The Key to Manufacturing Efficiency
In today’s competitive manufacturing landscape, improving efficiency and productivity is crucial for businesses to remain competitive. One of the key metrics used to measure manufacturing efficiency is OEE or Overall Equipment Effectiveness. In this blog, we will take a closer look at OEE and its importance in manufacturing.
How to Effectively Conduct a Legacy System Integration
Legacy system integration can be a daunting task, but it’s a necessary one for many manufacturers that rely on outdated systems to run their business. Integrating legacy systems with modern technology can improve efficiency, streamline processes, and save time and money. However, it’s important to approach the integration process carefully and methodically to ensure success.
Share on :
Keep On Reading
Subscribe to Our Newsletter
Subscribe to our weekly newsletters to get updates regarding our new production, behind the scene process of our art creation and much more.
After submitting this form you will receive an e-mail with a confirmation link that you must click to complete your request. Detailed information on processing and cancellation can be found in our privacy policy.
Lorem ipsum dolor sit amet, consectetur adipiscing elit. Ut elit tellus, luctus nec ullamcorper mattis, pulvinar dapibus leo.