How Modern SCADA Systems Are Transforming Manufacturing Operations
Blog
6 Min 44 Sec Read
Considering how SCADA began its journey in the 1960s, modern systems have come a long way. There was a time when they were being used as basic monitoring tools. But now, we are integrating SCADA systems with MES (Manufacturing Execution Systems) and other factory-based technologies. This shift isn’t just about better visualization – it’s about getting real-time control, predictive insights, and smart decision-making.
By using SCADA technology, manufacturers can optimize operations, reduce downtime, and improve performance-related efficiency like never before.
Thanks to advanced connectivity, automation, and real-time data analytics, SCADA in manufacturing is no longer just about tracking machines. Now, it focuses on transforming the entire production process. Let’s learn more about it.
The Evolution of SCADA Architecture
The usage of SCADA started as a basic monitoring and control tool and was used as is for almost four to five decades. However, now, it has evolved into a powerful backbone of industrial automation, which is designed to –
- Handle real-time analytics
- Make intelligent decisions
- Interconnect manufacturing operations
Modern SCADA system doesn’t just collect information. They drive efficiency, flexibility, and smarter workflows. Here’s what you need to know about the modern SCADA architecture and how it works –
Open Standards and Seamless Integration
Previously, most SCADA systems were created through rigid and proprietary protocols. However, today’s tools are built on open standards, which ensures better scalability and compatibility. Here’s what’s included in modern SCADA systems –
- OPC UA (Unified Architecture): A universal communication framework, which can be used for industrial automation.
- MQTT: A lightweight messaging protocol that allows you to exchange data efficiently in IIoT-based environments.
- SQL & RESTful APIs: Allow seamless integration with business systems and various third-party applications.
Platforms like Ignition and Tatsoft’s FrameworX have also been pushing open standards forward, which eliminates vendor lock-in effectively. As a manufacturer, you can also build adaptable, future-ready systems for your production factory.
Hybrid Deployment: On-Premises, Cloud, and Edge Computing
Like before, SCADA isn’t just a centralized system anymore. Modern SCADA systems use on-premises, cloud, and edge computing to maximize efficiency and resilience.
Here’s how –
- Critical control functions can be processed locally to minimize latency and ensure reliability in production and manufacturing
- Cloud-based SCADA enables advanced analytics, remote access, and large-scale data storage, which can be used for information collection
Edge computing, on the other hand, ensures continuous operations, even during network failures. And it does so by processing data closer to the source.
Leading SCADA platforms, like Inductive Automation’s Ignition, Siemens WinCC, GE’s iFIX, and Rockwell’s FactoryTalk have embraced this shift. They offer flexible, scalable solutions that fit everything from smaller plants to enterprise-wise developments.
Cybersecurity at the Core
With more connectivity, especially to the internet, comes more risk. And SCADA software is no exception. Cybersecurity is no longer an afterthought, and most modern SCADA systems come with the following tools to bolster their defenses –
- Multi-layered defense strategies can protect against cyberthreats
- Role-based access control and audit trails can ensure accountability and prevent threats coming from unauthorized access
- Encrypted communication and secure authentication will help with keeping data safe from security breaches
Seamless Integration: SCADA and MES Convergence
The traditional separation between MES and SCADA is disappearing rapidly. As factories keep embracing smart manufacturing, these systems are evolving into a unified operational technology and information technology stack. This enables you to make more intelligent and data-driven decision-making.
Bridging the OT/IT Divide
Modern SCADA systems serve as a critical link between industrial control systems and higher-level enterprise applications. Instead of merely monitoring your equipment, they can function as a real-time data conduit. So, you can use them to ensure seamless communication between machines, business systems, and MES platforms.
Here’s how –
- Live production data from control systems and PLCs flows directly into MES platforms by using a UNS model. This offers instant visibility and helps you synchronize different parts of your manufacturing plant effectively.
- MES-driven production orders are usually transformed into precise machine instructions through SCADA software. This optimizes workflow execution on the shop floor and gradually in the entire organization.
- Quality control data, which is gathered at the SCADA level, is automatically published to MES quality management modules. This supports real-time analysis and compliance tracking effectively.
- With a real-time Unified Namespace, manufacturers break down data silos, which can enable unprecedented visibility and operational coherence. It can be effective across the entire production environment.
Expanding Integration Beyond MES
Beyond MES, modern SCADA systems now seamlessly interact with a broader ecosystem of industrial applications. This forms a fully connected manufacturing infrastructure, which may include the following –
- Enterprise Resource Planning (ERP) Systems: This features a bi-directional integration with Oracle, SAP, and Microsoft Dynamics, which ensures that the production schedules are aligned with business objectives.
- Quality Management Systems (QMS): It focuses on automated data collection and real-time analysis support for defect detection and regulatory compliance.
- Predictive Maintenance Platforms: In this case, continuous condition monitoring helps detect equipment issues before failures can even occur. This can reduce downtime and maintenance-related expenses.
- Energy Maintenance Systems: SCADA-driven energy monitoring and optimization can improve efficiency and sustainability of your production plant.
By eliminating technological fragmentation and enabling a holistic, data-driven approach, modern SCADA systems are redefining how industrial control systems interact within a smart manufacturing ecosystem.
Real-World ROI: How Modern SCADA Systems Drive Measurable Success
The true value of modern SCADA systems isn’t just in their advanced form. It’s in the tangible impact they can offer on manufacturing performance and profitability. Businesses, especially the production plants, are using SCADA technology to increase their efficiency, quality, and cost savings. Here are some success stories you need to know regarding how SCADA has improved their productivity –
Case Study – 1: Automotive Parts Manufacturer
A tier-one automotive supplier modernized its industrial control systems by integrating Ignition SCADA with its Rockwell automation equipment and SAP ERP.
Here’s how the results looked like –
- 37% reduction in time spent on production reporting
- 45% fewer quality defects, thanks to real-time monitoring
- 22% increase in OEE (Overall Equipment Effectiveness)
The key to this success was how seamlessly data could get exchanged across shop-floor equipment, SCADA verification tools, and business systems.
Case Study – 2: Food & Beverage Manufacturer
A major beverage producer transitioned from a legacy SCADA system to a modern platform that provided direct MES integration. The outcome of this was striking –
- 15% boost in production throughput
- 28% reduction in unplanned downtime
- 33% increase in resource utilization
- 18-month payback period on the total investment
The upgrade they made centered on comprehensive data collection, predictive analytics, and mobile accessibility. This, in turn, empowered operators with real-time insights for faster issue resolution.
Best Practices for Implementing Modern SCADA Systems
Drawing from industry expertise and real-world success stories, manufacturers looking to modernize their industrial control systems must take a strategic, well-planned approach. Rushing into implementation without clear objectives can lead to inefficiencies, while a structured rollout ensures long-term success.
Here are the key best practices to follow.
Define Clear Objectives
Before investing in modern SCADA systems, you need to identify specific operational challenges they aim to resolve. Whether it’s about reducing downtime, improving real-time analytics, or improving regulatory compliance – having a well-defined goal helps in selecting the right technology and measuring ROI effectively.
Prioritize Open Standards
Flexibility is important when it comes to implementing a SCADA system. So, if you are considering integrating the same, choose an option that supports open protocols like OPC UA and MQTT. Open architectures will future proof your system but also enable seamless interaction with ERP, MES, and other enterprise applications.
Plan for System-Wide Integration
A well-structured SCADA Unified Namespace can ensure smooth data flow across all levels of smart manufacturing. However, before you integrate it, it’ll be important to assess how your SCADA solutions will interact with MES, ERP, Quality Management, and Maintenance Systems to create a cohesive digital ecosystem.
Implement in Phases
Instead of making an all-at-once rollout, you can start with pilot projects that deliver measurable improvements in a controlled environment. This phased approach can minimize disruptions, reduce risks, and allow you to adapt to the new technology.
Work with Experienced Integrators
Although Modern SCADA systems are inherently beneficial for every organization, integrating it can be difficult. So, partnering with a certified system integrator can ensure that both technology and manufacturing processes align seamlessly.
INS3: Your Trusted Partner in SCADA Modernization
Modernizing your industrial control system usually requires more than buying new technology. It demands expertise, hands-on experience, and industry certifications. At INS3, we bring all of these three to the table, making sure that you can seamlessly transition from older to a modern SCADA system. Here’s how we can help you out.
Certified Expertise across Leading SCADA Platforms
INS3 stands out as a trusted integration partner, as we hold certifications from some of the most recognized SCADA software providers in the industry.
- Ignition by Inductive Automation: Gold Certified Integrator
- GE Digital Solutions: Platinum Certified Partner (including iFIX, Proficy Historian, and Plant Applications)
- Tatsoft Certified Integrator: Extensive experience with Rockwell software, Aveva Wonderware, OSIsoft Pi, and others
Tailored Solutions for SCADA Modernization
Whether you are considering upgrading legacy systems or integrating SCADA with MES functionality, INS3 has the skills and strategic insights to assist you.
Here’s what our approach ensures –
- Seamless integration with existing enterprise systems
- Optimization for smart manufacturing, improving efficiency, and real-time decision-making
- Implementation of industry best practices by using cutting-edge modern SCADA systems
The future of industrial automation is evolving rapidly. So, staying ahead in the market is going to require proactive innovation. With INS3, you can modernize your SCADA infrastructure and position your manufacturing operations for long-term success.
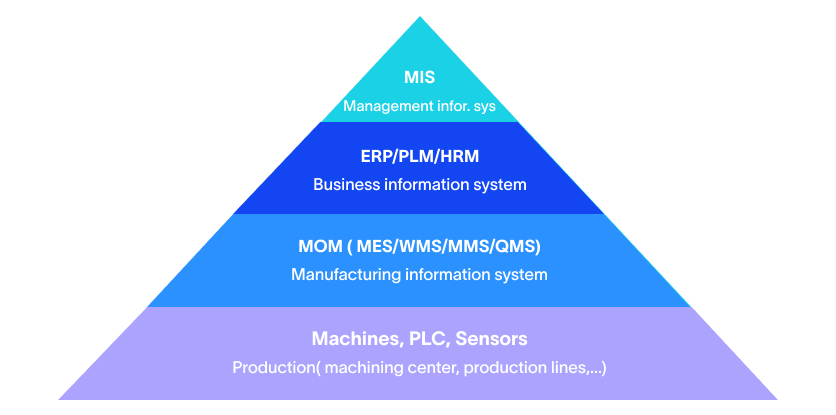
Agile MES: The Key to Unlocking Smart Manufacturing Success
MES is a computerized system used in manufacturing operations to track and document the transformation of raw materials into finished goods. An MES system typically manages and monitors work orders, equipment, materials, and personnel on the shop floor. The system provides real-time visibility into production processes, helps optimize manufacturing operations, and improves the overall efficiency of the manufacturing process.
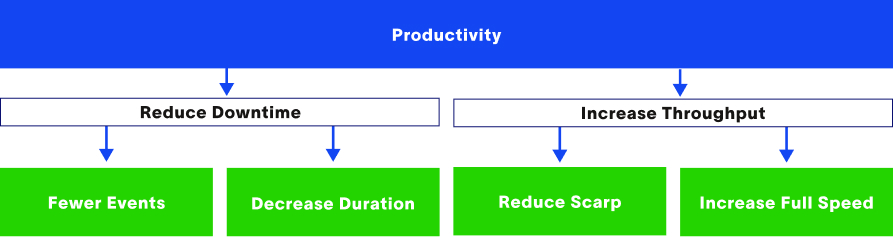
Understanding OEE: The Key to Manufacturing Efficiency
In today’s competitive manufacturing landscape, improving efficiency and productivity is crucial for businesses to remain competitive. One of the key metrics used to measure manufacturing efficiency is OEE or Overall Equipment Effectiveness. In this blog, we will take a closer look at OEE and its importance in manufacturing.
How to Effectively Conduct a Legacy System Integration
Legacy system integration can be a daunting task, but it’s a necessary one for many manufacturers that rely on outdated systems to run their business. Integrating legacy systems with modern technology can improve efficiency, streamline processes, and save time and money. However, it’s important to approach the integration process carefully and methodically to ensure success.
Share on :
Keep On Reading
Subscribe to Our Newsletter
Subscribe to our weekly newsletters to get updates regarding our new production, behind the scene process of our art creation and much more.
After submitting this form you will receive an e-mail with a confirmation link that you must click to complete your request. Detailed information on processing and cancellation can be found in our privacy policy.