The Power of Real-Time Manufacturing Data - MES Connectivity
Blog
6 Min 29 Sec Read
Manufacturing Execution Systems (MES) connect enterprise planning systems with shop floor operations to generate real-time manufacturing data.
While traditional MES implementations help manage production, their connectivity to actual production processes is actually what determines the usability.
When you have access to real-time connectivity, you can transform your MES from being a basic record-keeping tool to a dynamic operational system that helps improve your manufacturing performance.
The Evolution of MES Connectivity for Real-Time Manufacturing Data
Traditional MES implementations or lack of MES often operate with significant data delays. Information typically flows from production to the MES through manual entry, scheduled transfers, or end-of-shift uploads. These delays create several problems:
- It can slow the response system for production issues
- Creates discrepancies in tracking WIP
- Fails to manage reactive quality
- Limits real-time optimization
- Blocks operational visibility for real-time manufacturing data
As Walker Reynolds, a thought leader in industrial automation, notes: “The digital transformation of manufacturing depends on the unification of data, with real-time connectivity being the foundation. Without it, you’re making decisions based on history rather than reality.”
The Three Pillars of Modern MES Integration
According to the framework established by INS3’s experience and other industry experts, effective MES integration rests on three fundamental pillars:
Real-Time Connectivity
Real-time connectivity establishes direct, immediate data exchange between equipment and MES, enabling smart manufacturing using the following datasets and functions:
- Real-time reporting of units, cycles, and rejects
- Live quality data needed for real-time monitoring
- Flexible scheduling to enable process support according to real-time changing conditions
- Current equipment status immediately available to determine the current state and alarms
- Two-way talk to give instructions and feedback with real-time manufacturing data
Industrial communication infrastructure of this new type needed:
- OPC UA for interoperable equipment communication
- Edge computing for local computation
- MQTT for low-weight, reliable messaging
- Secure IT/OT network integration
Combined Time-Series and Event Data
Good manufacturing intelligence considers both continuous time-series and production event data. Contemporary MES implementations combine them into a combined historical record that yields real-time manufacturing data:
Time-Series Data records continuous variables such as temperature, pressure, speed, and power usage with accurate timestamps. This information enables:
- Process behavior trend analysis
- Correlation of operating parameters to quality results
- Early detection of equipment deterioration
- Establishment of baseline for normal operation
MES Event Data records some manufacturing events such as:
- Downtime events and causes
- Quality failures and inspection results
- Batch start/finish milestones
- Material movements and consumption
- Order status updates
- Production quantity and waste events
- OEE calculation triggers
- Operator actions and comments
The combination of these complementary data types assists in filling gaps as follows:
- Time-series data reflects what occurred during continuous processes
- Event data reports why something happened and its implication on operations
- Both, individually, are not complete digital histories that enable more informed decision-making
This integrated solution has unequivocal benefits compared to conventional databases:
- Effective storage with proper handling of each type of data
- Contextual correlations among process conditions and manufacturing events
- Total traceability from material through manufacture
Unified Namespace Architecture
The unified namespace concept, championed by Walker Reynolds, provides a standardized addressing scheme for all manufacturing data. This architecture delivers:
- Decoupled systems to help equipment and applications to evolve independently
- Simplified integration where systems connect to one namespace and not multiple points
- Consistent data access to crate standardized methods for all information
- Contextual relationships to clarify hierarchies between data points
- Future-proofed infrastructure where new technology integrates without disruption
A well-designed unified namespace often leverages the ISA-95 Part 2 model, which defines a standard hierarchy for manufacturing operations:
Enterprise/Site/Area/WorkCenter/WorkUnit/Equipment/Control
This ISA-95 based structure creates an intuitive addressing scheme where we follow the standards of the industry:
company/plant/process_area/production_line/machine/component/data_point
For example, a temperature sensor on an extruder in a plastics operation might be addressed as:
acme/cleveland/injection/line3/extruder2/barrel/zone1/temperature
This hierarchical approach as per ISA-95 stipulates that real-time manufacturing data and information in real fact are properly established in context and rendered readily accessible to all the systems. It does not lose track of the intricate mapping of myriad naming conventions together with industry-determined standards.
The Business Impact of Real-Time MES Integration
These three pillars of MES integration can deliver substantial business benefits:
Efficiency Gains
- Improving 30-50% changeover with real-time manufacturing data for delivery of instructions
- Lowering downtime by 25-45% with instant reporting of issues
- Improving 15-25% scheduling with higher throughput by responding to actual conditions
- Lowering WIP by 20-40% through precise tracking
Quality Improvements
- Reducing defects by 30-60% with in-process monitoring
- Containing issues before they spread downstream
- Optimizing process parameters within limits
- Clear tracking of materials and parameters and aligning them with finished goods
Visibility Benefits
- Single source of truth with one data set for everyone
- Real-time dashboards that display your status in real time and make it visible throughout the organization
- Informed decision-making with real-time manufacturing data and eliminating estimation theories
- Enabling remote monitoring
Cost Reductions
- Lowering 10-20% labor costs through data collection automation
- Decreasing 20-35% costs through reduced scrap, rework, and warranty claims
- Optimizing 15-25% maintenance with condition-based strategies to save costs
- Saving 5-15% energy through process optimization
Implementation Approach
Effective MES connectivity for us is a 4-step process whereby you leverage what you have today in technology wherever possible. Moreover, we clearly define our objectives, pilot the idea and then deploy our solutions.
That’s how we sequence our implementation process to facilitate smart manufacturing online for our customers and provide real-time manufacturing data:
Asset Connectivity
- Inventory all production equipment and assess connectivity options
- Select appropriate protocols for each equipment type
- Deploy edge infrastructure at the equipment level
- Test and validate data flow from connected assets
Historian & Event Framework
- Define data collection strategy (points, frequency, events)
- Implement storage with appropriate retention policies
- Configure event triggers for MES transactions
- Validate data collection accuracy and completeness
Unified Namespace
- Design logical structure and naming conventions
- Deploy message broker infrastructure
- Plan migration from point-to-point connections
- Establish standard publish/subscribe patterns
MES Integration
- Map MES functions to real-time data requirements
- Connect MES data structures to the unified namespace
- Optimize workflows to leverage real-time capabilities
- Develop effective user interfaces for real-time information
This progressive approach transforms disconnected systems into an integrated manufacturing ecosystem.
INS3: Expertise in Real-Time MES Integration
INS3 is dedicated to integrating MES systems with shop floor activities using factory automation and smart manufacturing enabled by real-time integration. Our strategy is to integrate deep process understanding of manufacturing with industrial technology expertise in enabling measurable business outcomes.
Machine-Level Understanding
Our engineers bring practical shop floor experience across diverse industries. Here’s a glimpse of our grasp in delivering real-time manufacturing data through different platforms and technology:
- PLC integration expertise with Allen-Bradley, Siemens, Mitsubishi, and other platforms
- Protocol proficiency from traditional Modbus to modern OPC UA and MQTT
- Machine behavior analysis to identify critical parameters for effective monitoring
- Local data processing with edge computing
This expertise ensures our integrations capture the right information in the right way, creating a solid foundation for MES connectivity.
Comprehensive MES Requirements Analysis
We analyze manufacturing operations holistically to help align with your real-time manufacturing data:
- Process mapping to identify information flows and decision points
- Data requirements for effective production management
- KPI alignment to ensure metrics drive improvement
- Compliance documentation for regulated industries
At INS3, we begin by knowing the data that influences manufacturing performance and subsequently deploy MES solutions to provide real business value.
Proven Results Across Industries
Our real-time MES integrations have consistently delivered results:
- 15-30% increase in overall equipment effectiveness
- Up to 45% reduction in defect rates through real-time monitoring
- Complete shop floor transparency with real-time dashboards
- 10-25% decrease in total operational costs
These results come from our implementation of all three pillars: real-time connectivity, integrated time-series and event data, and unified namespace architecture.
Strategic Partnership Approach
At INS3, we work hand in hand with our clients to develop sustainable solutions that yield better outcomes. We ground our practice on phased implementation to provide certain milestones for gauging progress.
Moreover, using different knowledge transfer techniques we enable our clients to develop their internal capacity, fostering a culture of ongoing improvement driven by operations feedback.
Also, our emphasis on technology road mapping helps you identify future improvements, keeping our clients ahead during the changing world of manufacturing.
This strategy helps your manufacturing business attain short-term success as well as establish foundations for long-term greatness in their operations.
The Time for Real-Time is Now!
The MES-shop floor disconnect is a problem and also an opportunity for today’s producers. Through real-time connectivity, combined time-series and event data, and a common namespace architecture, you can convert separate operations into coordinated, data-enabled production systems.
Digital transformation of manufacturing isn’t installing more technology. It means the way you tie and put in context the technology you already use to drive live manufacturing data and leverage the same to attain business excellence.
Accordingly, then, at INS3, we calibrate our strategy based on these findings and your current technology and build relationships that bring you measurable gains in your efficiency, quality, visibility, and cost.
Whether you are beginning your digital transformation effort or refining existing infrastructure, INS3 offers the technical support necessary to make the transition between your MES connectivity and shop floor activities seamless. With our extensive knowledge of both machine-level integration and MES needs, we offer implementations that bring both rapid return and long-term competitive edge through real-time manufacturing information.
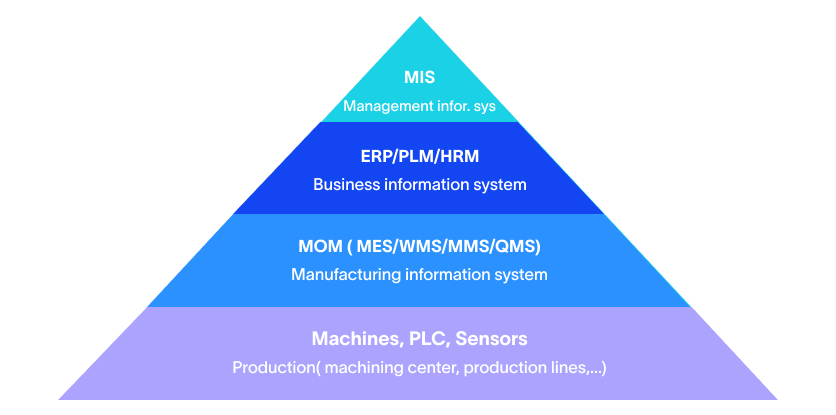
Agile MES: The Key to Unlocking Smart Manufacturing Success
MES is a computerized system used in manufacturing operations to track and document the transformation of raw materials into finished goods. An MES system typically manages and monitors work orders, equipment, materials, and personnel on the shop floor. The system provides real-time visibility into production processes, helps optimize manufacturing operations, and improves the overall efficiency of the manufacturing process.
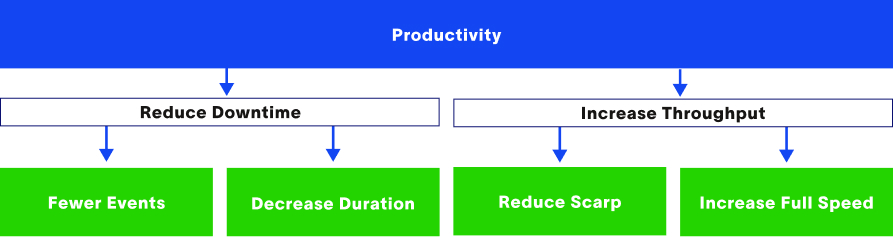
Understanding OEE: The Key to Manufacturing Efficiency
In today’s competitive manufacturing landscape, improving efficiency and productivity is crucial for businesses to remain competitive. One of the key metrics used to measure manufacturing efficiency is OEE or Overall Equipment Effectiveness. In this blog, we will take a closer look at OEE and its importance in manufacturing.
How to Effectively Conduct a Legacy System Integration
Legacy system integration can be a daunting task, but it’s a necessary one for many manufacturers that rely on outdated systems to run their business. Integrating legacy systems with modern technology can improve efficiency, streamline processes, and save time and money. However, it’s important to approach the integration process carefully and methodically to ensure success.
Share on :
Keep On Reading
Subscribe to Our Newsletter
Subscribe to our weekly newsletters to get updates regarding our new production, behind the scene process of our art creation and much more.
After submitting this form you will receive an e-mail with a confirmation link that you must click to complete your request. Detailed information on processing and cancellation can be found in our privacy policy.