Manufacturing Cost Optimization: Using Technology to Drive Profitability
Blog
5 Min Read
Rising operational costs in the manufacturing industry are one of the worst outcomes of inflation, labor expenses, and material prices. Ironically, this higher manufacturing cost can become a cyclic pattern causing the above-mentioned factors to rise further. Years into this cycle have resulted in a broader economic shift.
At this point, technology appears to be the savior with the potential to break this cycle.
Reducing manufacturing costs is a priority, and manufacturers are adopting effective technologies to address this issue.
By implementing lean practices, you can now optimize production processes, eliminate waste, and enhance resource utilization, leading to reduced costs and improved product quality.
However, to reduce costs with the help of technology, it is important to align the anti-heroes and the heroes. Hence, we must figure out what cost can be reduced by what technology.
This guide will help you understand exactly that so you can find the right technology and help your business in reducing manufacturing costs.
Hidden Cost Factors in Manufacturing Operations
Hidden costs, as you know, are the ones that do not reflect in your standard financial reports. However, they significantly affect your profitability and efficiency.
These costs stem from inefficiencies like rework, scrap, downtime, and underutilization of resources. If you ignore these hidden costs, it can lead your profit margins to erode, slow your production process, and delay the deliveries. Thus, bringing the worst outcome, damaged customer relationships.
So, let us take a deeper look at the potential hidden costs in a manufacturing industry where technology can have a huge positive impact.
Inefficient Processes
Inefficient processes lead to wasted time and resources. Hence, it increases your operational costs.
These inefficiencies arise from outdated machinery, poorly designed workflows, or lack of automation. The result is often longer production times and higher labor costs. It erodes profit margins.
Equipment Downtime
Unplanned equipment downtime is a major hidden cost that hampers your efforts for reducing manufacturing costs. This factor majorly affects production schedules and revenue.
When a machine fails unexpectedly, it can halt the entire production line. Thus, it becomes unavoidable to reduce delays and labor costs as workers wait for repairs.
According to industry estimates, downtime can cost manufacturers thousands of dollars per hour.
Lean manufacturing techniques such as predictive maintenance can help anticipate equipment failures before they occur, reducing downtime and associated costs significantly.
Quality Control Issues
Quality control issues can lead to substantial financial losses of 15%-20% of sales revenue.
As you already know, defective products require rework or scrapping. But this extra work increases material waste and labor costs.
Additionally, poor quality can harm your brand’s entire reputation by aggravating your customers. Thus, you can face the problem of lost sales and increased warranty claims.
Thus, it is important to leverage quality control systems to minimize these risks by catching defects early in the production process.
Inventory Management Inefficiencies
Ineffective inventory management may lead to an oversupply of products or shortages, both of which can constrain your capital and hinder production timelines.
While an excess of inventory results in increased storage expenses and the possibility of items becoming outdated, shortages lead to you losing sales opportunities.
Thus, you can use robust inventory management software to streamline stock levels. These systems provide you with real-time demand information, thereby lowering carrying costs and enhancing cash flow.
Data Silos
Data silos arise when information remains isolated within individual departments, resulting in poor decision-making and a lack of efficiency.
This disconnection can hinder you from discovering cost-saving opportunities and even reacting to shifts in the market.
An integrated data management system can enhance visibility throughout your operations, enabling improved decision-making and reducing manufacturing costs.
Supply Chain Disruptions
Data silos emerge when information is confined within specific departments. It leads to misguided decision-making and decreased efficiency.
Moreover, data silos cause a disconnection that obstructs you from uncovering cost-saving opportunities or promptly addressing market fluctuations.
By embracing integrated data management systems, you can augment visibility across your operations. This foster enhanced decision-making and alleviates your operational inefficiencies.
Labor-Related Costs
Labor-related expenses extend beyond mere salaries. This is where you must include all the extra costs associated with training, overtime, and inefficiencies that stem from ineffective workforce management.
When you fail to put your human resources to its maximum benefit, you automatically become prone to higher operational costs. However, this is one of those expenditures that might not be evident at first glance.
Implementing technologies like workforce management systems take your productivity to heights while you can smoothly optimize labor allocation.
This ensures that human resources are used effectively, while simultaneously reducing unnecessary expenditures.
How MES, SCADA, and IIoT Reduce Operational Costs?
The integration of SCADA, MES and IIoT technologies forms a comprehensive framework that significantly reduces operational costs in manufacturing. Together, these systems enhance visibility, boost efficiency, and facilitate informed decision-making, allowing manufacturers to achieve substantial cost savings and improved competitiveness in an increasingly challenging market landscape.
MES + SCADA + IIoT
MES offers real-time visibility into production processes, allowing you to continuously monitor activities and equipment status. By making workflows and resource allocation more streamlined, this system reduces downtime and waste. Thus, reducing manufacturing costs up to 30%.
This efficiency stems from features such as automated scheduling and immediate data analytics, which help adjust production plans dynamically, thereby increasing throughput.
As a continuity, SCADA systems support MES by providing centralized control of industrial processes.
This duo can monitor how your equipment performs and its environmental conditions in real time. Thus, you can find prompt responses to anomalies.
Thus, you can minimize the risk of equipment failures that could lead to costly unplanned downtimes.
By enhancing data collection and analytics, SCADA systems, when integrated with MES, contribute to a cohesive operational strategy that drives further cost reductions through maintenance optimization and improved efficiency.
To make the circle complete, you can use IIoT to enhance the functions of both MES and SCADA.
This system connects devices across the manufacturing floor that allows for the collection of extensive data. You can analyze this data to see where you’re lagging and optimize the operations accordingly.
Moreover, predictive maintenance powered by IIoT sensors can anticipate equipment failures, significantly reducing downtime and associated maintenance costs. Also, IIoT supports real-time inventory management, ensuring accurate material tracking throughout the production cycle.
Thus, with the power of three, you can minimize excess inventory and carrying costs while maintaining uninterrupted production schedules and reducing manufacturing costs.
How to Calculate ROI from Digital Transformation?
Here are the steps that help you calculate ROI from digital transformation for reducing manufacturing costs:
1. Identify the following costs:
- Initial Costs
- Setup Costs
- Training Costs
- Maintenance
- Other Costs
2. Identify the following benefits:
- Increased Efficiency
- Reduced Downtime
- Lower Operational Costs
- Improved Quality
- Enhanced Customer Satisfaction
- Increased Revenue
3. Quantify the benefits by converting them to monetary values (e.g., savings from reduced downtime).
4. Calculate net benefits with the following equation:
Net Benefits = Total Benefits – Total Costs
5. Calculate ROI with the final equation:
ROI = (Net Benefits / Total Costs) × 100%
Example of ROI Calculation with Lean Manufacturing Techniques
- Costs: $100,000 (initial) + $20,000 (additional) = $120,000
- Benefits: $150,000
- Net Benefits: $150,000 – $120,000 = $30,000
- ROI: (30,000 / 120,000) × 100% = 25%
For this, you can use ROI calculators like SCW.AI’s Digital Factory ROI Calculator for structured estimates.
Improve Cost Efficiency with Technology
Navigating the complexities of reducing manufacturing costs is all you need to maintain competitiveness in the market.
By embracing lean manufacturing cost savings and prioritizing manufacturing process optimization, you can effectively identify and eliminate hidden costs that hinder profitability.
Integrating advanced technologies streamlines operations and unlocks opportunities for greater efficiency and productivity.
As you take steps to transform your manufacturing practices, remember that investing in the right solutions will pay dividends in enhanced product quality, improved customer relationships, and a stronger bottom line.
It’s time to break the cycle and position your business for sustainable success!
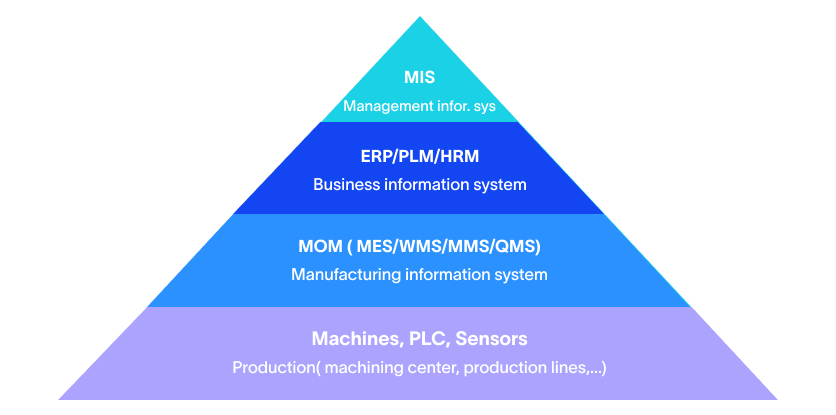
Agile MES: The Key to Unlocking Smart Manufacturing Success
MES is a computerized system used in manufacturing operations to track and document the transformation of raw materials into finished goods. An MES system typically manages and monitors work orders, equipment, materials, and personnel on the shop floor. The system provides real-time visibility into production processes, helps optimize manufacturing operations, and improves the overall efficiency of the manufacturing process.
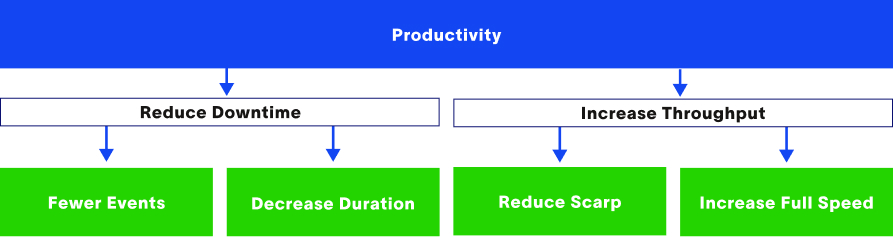
Understanding OEE: The Key to Manufacturing Efficiency
In today’s competitive manufacturing landscape, improving efficiency and productivity is crucial for businesses to remain competitive. One of the key metrics used to measure manufacturing efficiency is OEE or Overall Equipment Effectiveness. In this blog, we will take a closer look at OEE and its importance in manufacturing.
How to Effectively Conduct a Legacy System Integration
Legacy system integration can be a daunting task, but it’s a necessary one for many manufacturers that rely on outdated systems to run their business. Integrating legacy systems with modern technology can improve efficiency, streamline processes, and save time and money. However, it’s important to approach the integration process carefully and methodically to ensure success.
Share on :
Keep On Reading
Subscribe to Our Newsletter
Subscribe to our weekly newsletters to get updates regarding our new production, behind the scene process of our art creation and much more.
After submitting this form you will receive an e-mail with a confirmation link that you must click to complete your request. Detailed information on processing and cancellation can be found in our privacy policy.